Native plants didn't need to be planted for this growth, all that was needed was to remove the invasive plant species.
Sustainable plant of the year
Laying a Model
of Sustainability for Food Processing
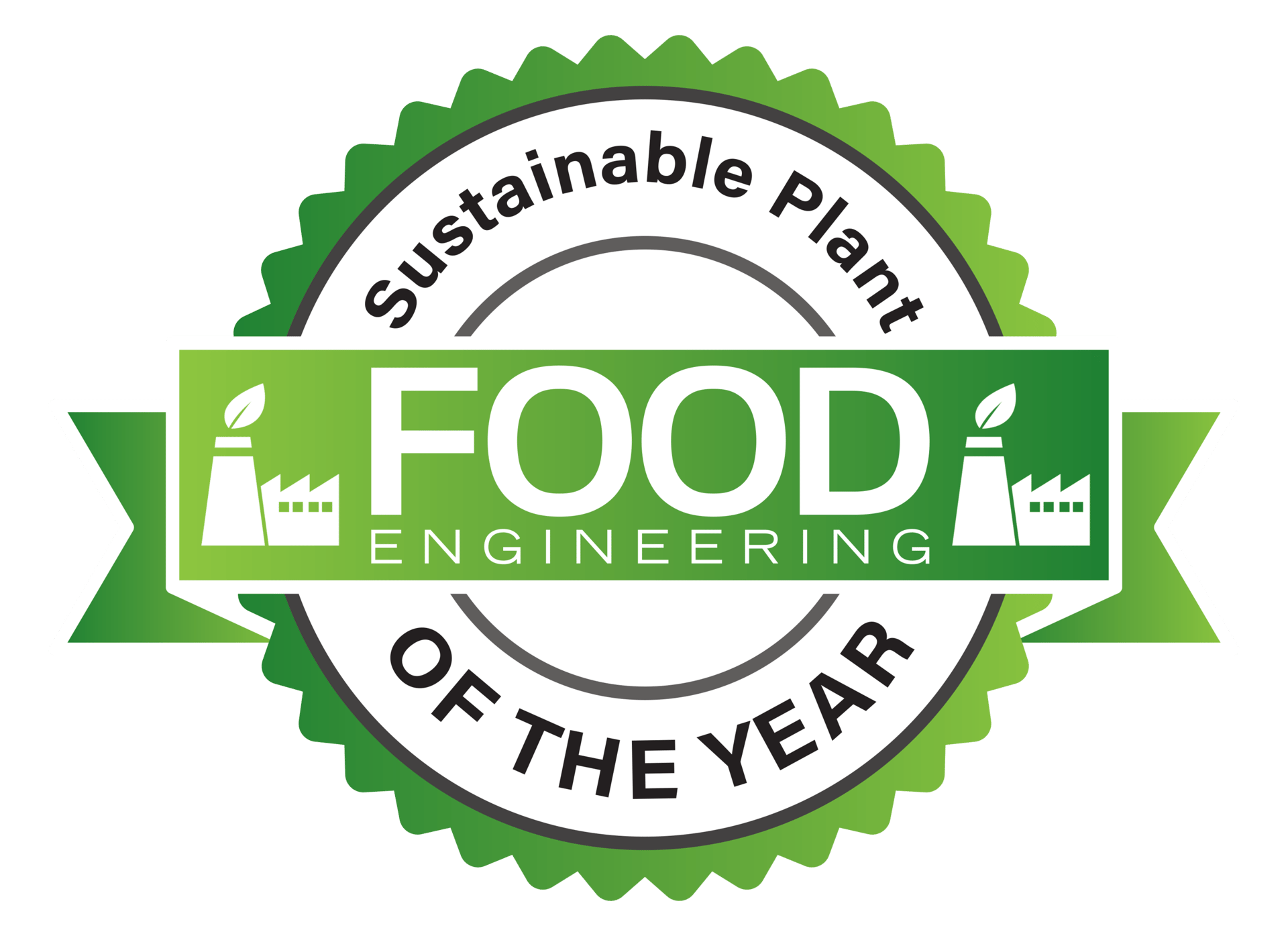
Vital Farms hatched a plan to create a model of sustainability for Egg Central Station, which is why it’s FOOD ENGINEERING’s 2023 Sustainable Plant of the Year.
All images courtesy of Vital Farms
It only takes a few seconds after stepping into Vital Farms’ Egg Central Station (ECS) to realize that the company truly loves its egg-related puns. If there’s writing nearby, be it on a wall, memo or bulletin board, there’s a pun not far behind. They’re part of an ethos that starts from the top and flows down the company’s ranks to put a smile on someone’s face, even if just for a second. That idea of doing good extends beyond the facility walls to its other locations, the farmers who supply the eggs, the consumers who buy the product and, finally, to the planet itself. That visible commitment to the environment is why the addition at ECS was chosen as FOOD ENGINEERING’s 2023 Sustainable Plant of the Year.
Located in Springfield, Mo., the original 85,000-sq.-ft. ECS opened in 2017, comprising a 65,000-sq.-ft. production floor and 20,000-sq.-ft. administrative space. The addition completed in May 2022 added another 65,000-sq.-ft. production space, mirroring the original in its design. Doubling the production space with an identical floor plan benefitted the company by allowing it to double throughput—going from processing three million eggs per day to six million.
“When we built the original facility, we knew that we were going to need additional capacity at some at some point,” says Carl Kicklighter, director of plant operations at Vital Farms. “I think it maybe came a little quicker than what we had originally planned, which is great problem to have.”
All of Vital Farms’ eggs are processed at ECS and then shipped to every state in the continental U.S. This is part of the reason why the Springfield location wasn’t a shoo-in for the site when the decision was made to add capacity. “It just so happened to be that this is ultimately what we chose,” says Kicklighter. “Once we were here and integrated into the community, it became obvious pretty quickly that this is ultimately where we wanted to add to. And then came the decision of ‘Do we add on this particular piece of property? Do we buy a neighboring piece of property?’ Once we worked through that, it ultimately landed that the expansion project is what we would go with.”
by DERRICK Teal, Editor-in-Chief
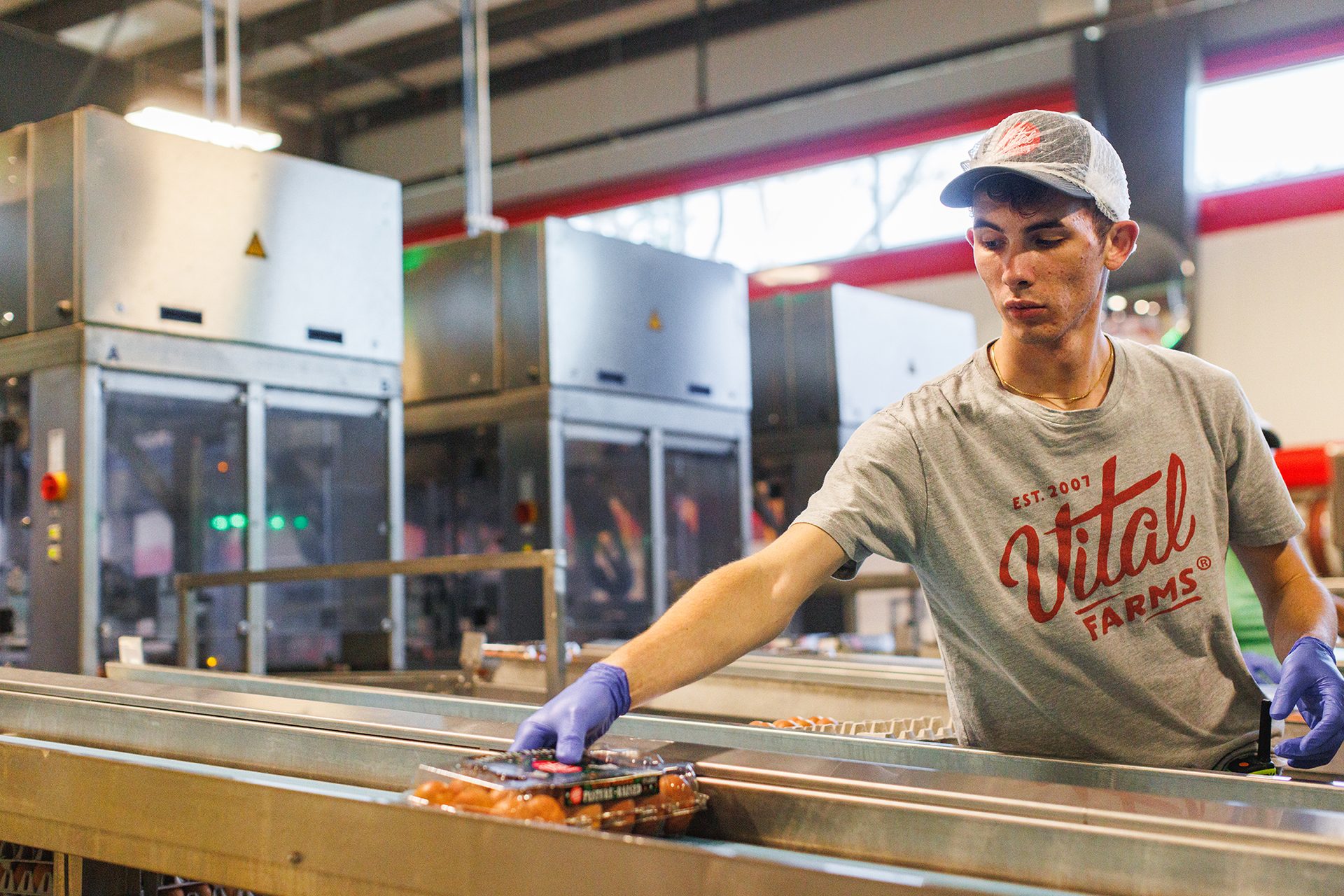
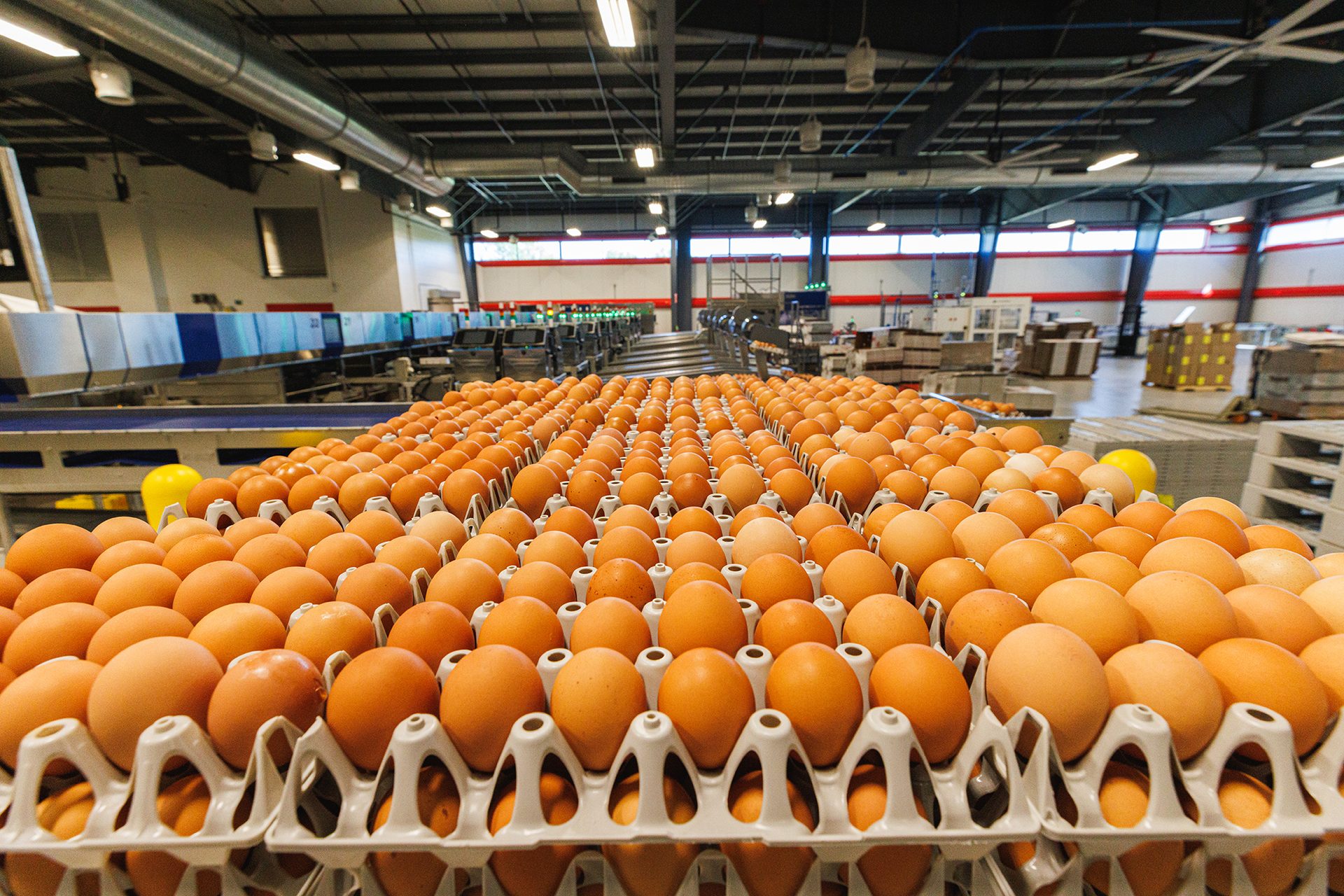
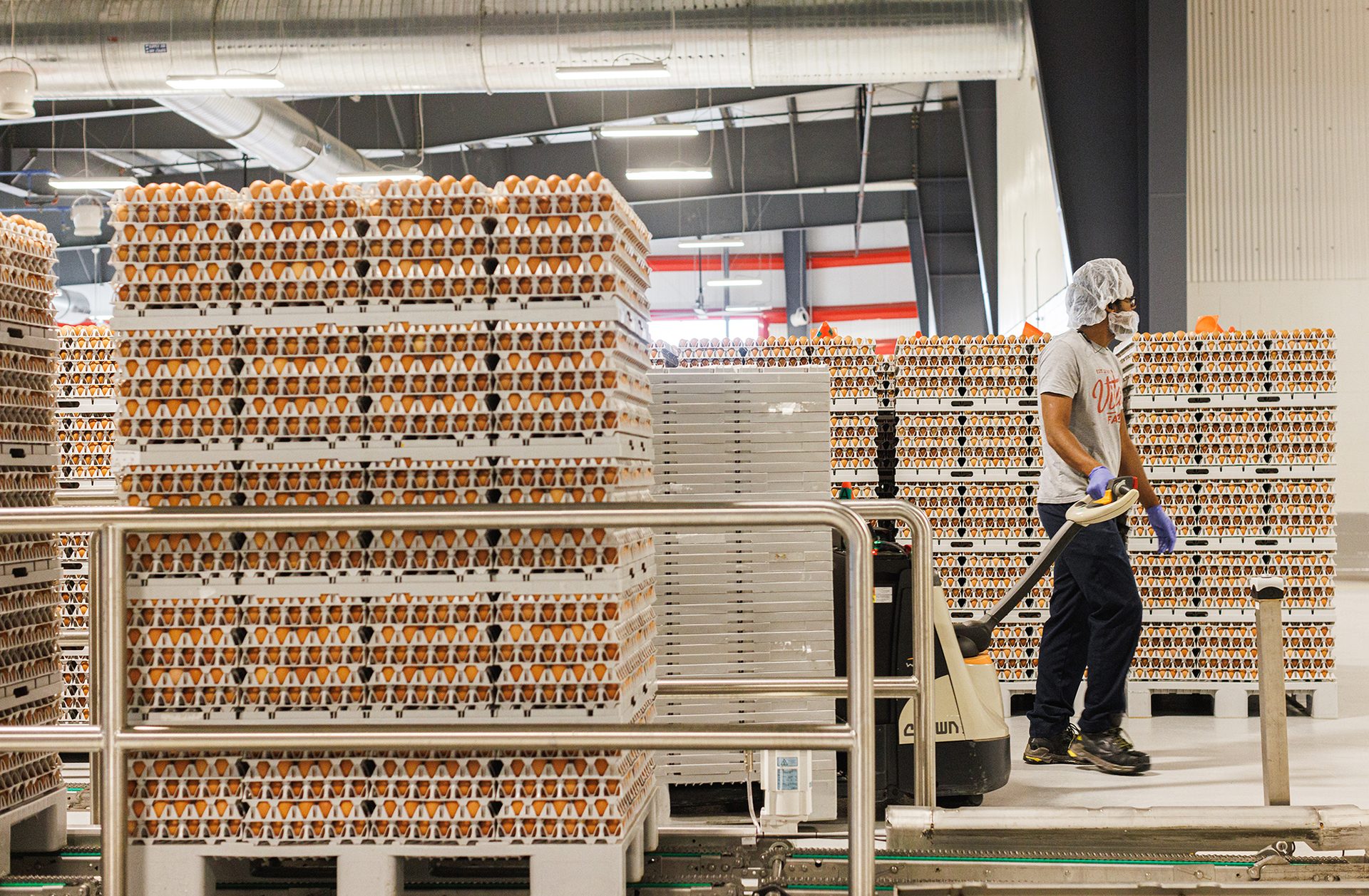
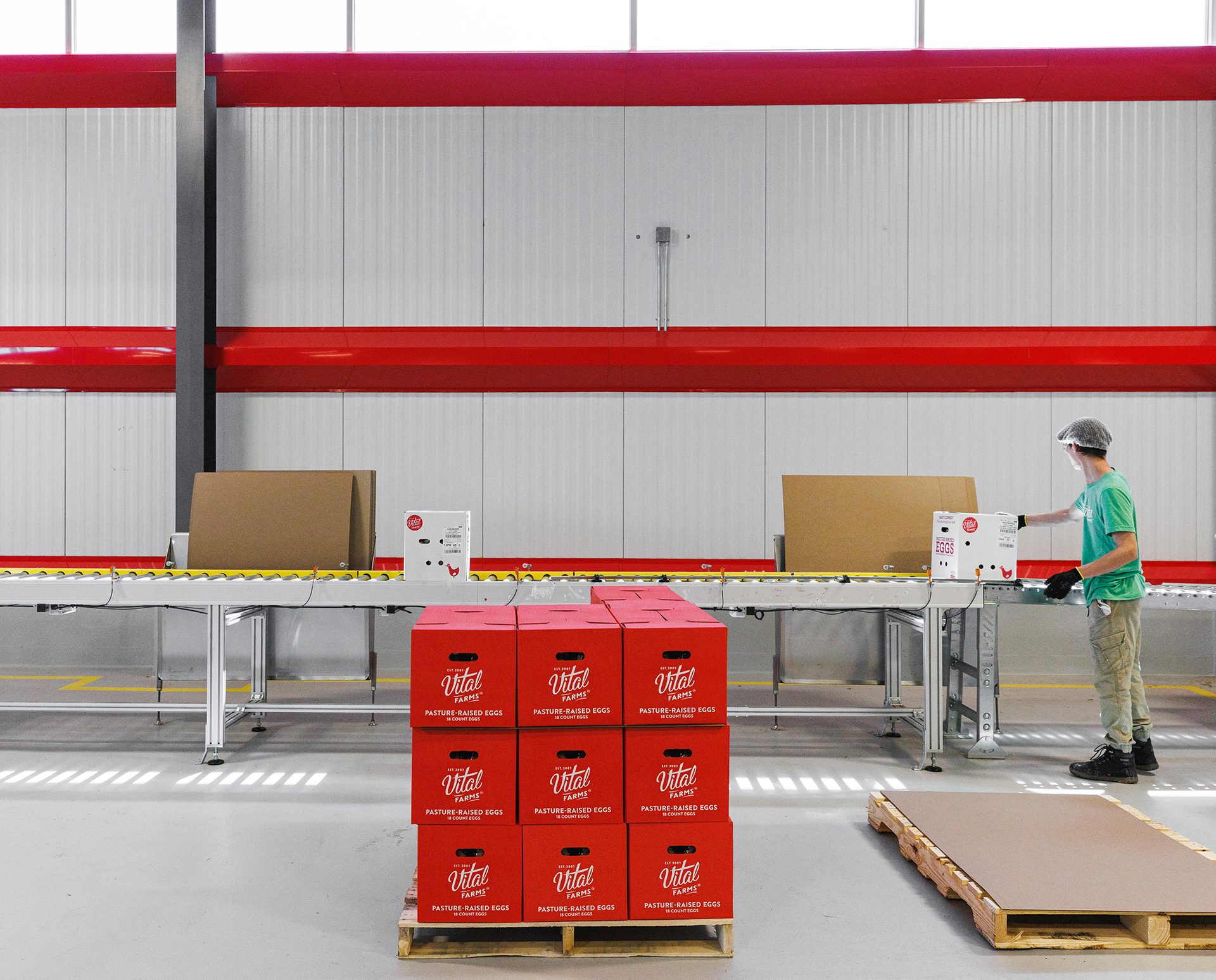
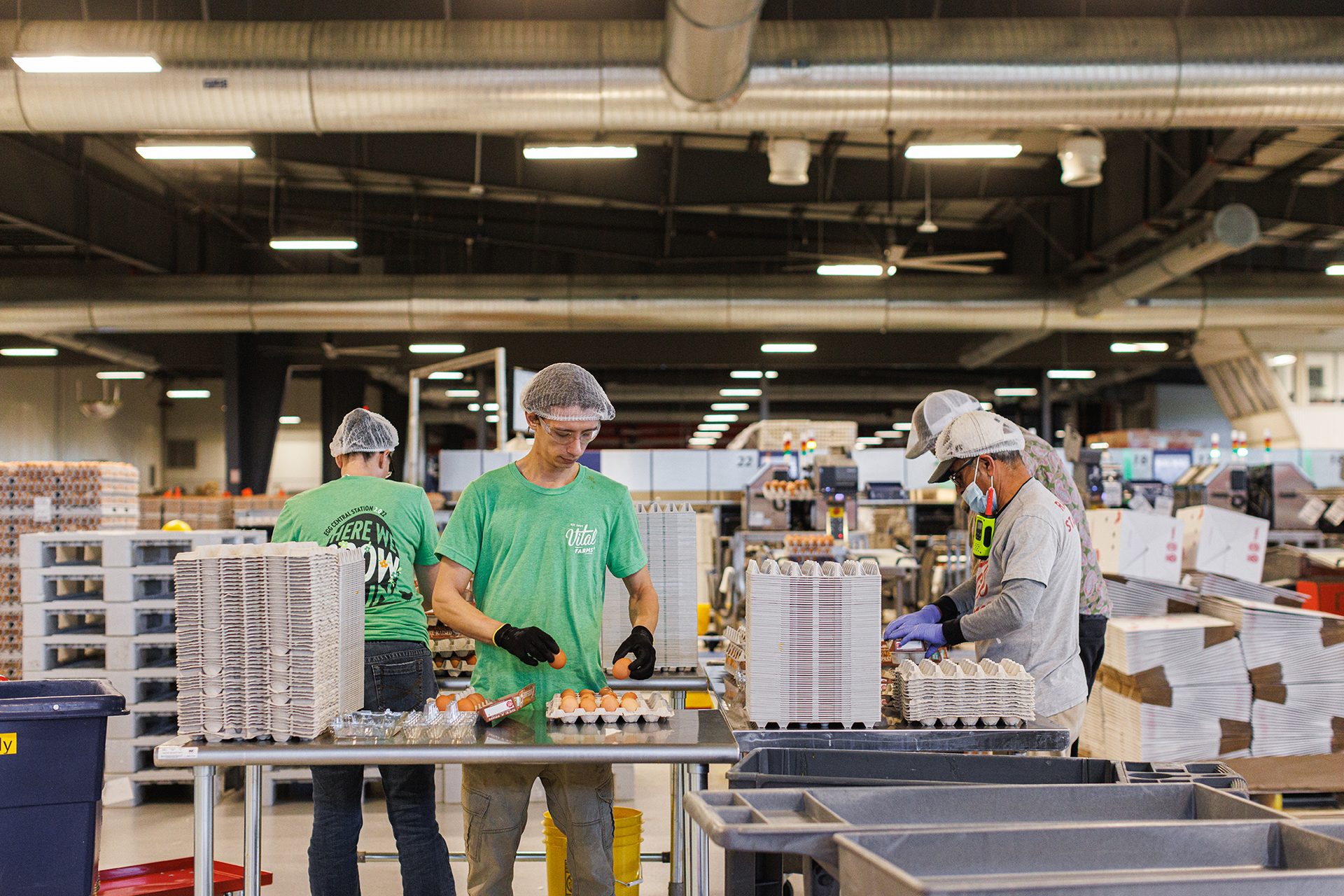
The production floor of Vital Farms' Egg Central Station is an open, light-filled space designed as much to benefit employees with pleasant working conditions as it is to benefit the environment.
The White
Because so much is shipped from the site, particular attention was paid to the shipping docks. ECS is able to turn approximately 50 semis per day (25 in and 25 out) as eggs are shuttled back and forth from a nearby 2 million-sq.-ft. cold-storage facility (aka, a cave) called Springfield Underground. This facility allows the eggs to be cooled using minimal energy and provide the company with cost and energy savings. The dock area is actively heated for worker comfort during the winter months, but it uses the natural cooling offered by the concrete floors in warmer months. Insulated metal panels comprise the shell of the facility and preserve the conditioned interior air with high R-values and a tight envelope while limiting the heating effects of direct sunlight. Trucks back into the bays, right up to the door, where a seal is created with the dock before the trailer doors are opened to minimize the amount of conditioned air lost from the refrigerated trailer. Additionally, spacing between bays is four feet instead of two, with the idea that the additional space creates more room for door and forklift operations. From there, the eggs are taken off of the truck and moved to a cold storage room to await processing.
Vital Farms’ efforts at improving employee welfare surround the plant floor, even if they’re not what first jump to mind when walking in. Clerestory windows top two of the four walls in the processing section, and very few columns in the space enable plenty of natural light to shine through. Natural light and visible sightlines to the outside have been demonstrated to improve wellbeing, which is why many healthcare providers are including windows wherever possible to speed patient healing. While Vital Farms isn’t necessarily helping people to convalesce at its plant, the idea of nature benefitting its staff is clearly a goal. The processing floor feels much more airy because of that lack of walls and columns, and avoids that oppressive feeling that can sometimes be felt in plants with many columns and walls with no natural light. Artificial light at ECS comes from energy-efficient LEDs.
Air movement is also an essential component. In the office portion of the plant, Kicklighter says that a lot of consideration went into eliminating the buildup of CO2 that occurs throughout the day. The first thought one might have to solve that problem would be to remove the source of that CO2 emission, but it’s difficult when that source is the primary focus of the office: people. While a buildup of CO2 caused by people breathing wouldn’t necessarily be an issue in a space as large as Vital Farms’ processing floor, pockets of hot and cold air can still be created even with the most thoughtfully placed HVAC systems. Helping to mitigate that and create more evenly distributed temperatures throughout, which also creates a more energy-efficient and comfortable space, are large ceiling fans that slowly rotate but rotate fast enough to push large amounts of air. Materials used to construct the facility contain high recycled content and are made with low volatile organic compounds (VOCs) to also help improve indoor air quality (IAQ).
“At the end of the day, we want more people to hear our story—and it's not in an arrogant or egotistical way. We think we can be a model for people to follow.” — Carl Kicklighter, director of plant operations
The Yolk
The speed at which the Moba-supplied machinery moves the eggs through the process of cleaning, testing, sorting and packaging is truly impressive. When talking about a goal of processing up to six million eggs per day, everything has to move fast. But, there are probably people out there who experience more breakage moving their eggs from the refrigerator to the counter than what Vital Farms experiences moving eggs from cold storage on through to being packaged. Not only is this good for business, but it’s good for the environment given how much it's affected by food wastage.
Despite the speed, Vital Farms expects its products to meet the highest standard of food safety requirements. ECS has achieved Safe Quality Food, or SQF, Level 3 certification, the highest level of such certification from the Global Food Safety Initiative. Vital Farms is also one of the few members of the SQF “Select Site” program, meaning the company is prepared for a safety audit on its facilities to take place at any time. Egg Central Station is the only egg facility in the world that's SQF Select certified and one of only a few facilities in the world that has this certification.
So when it comes time to clean the eggs, the area where the eggs are washed is physically separated from the rest of the processing. Dirty eggs enter and are washed with 100°F water that a filtration system recaptures, filters and reuses, under the proper USDA guidelines, to minimize water use.
The eggs then pass into a drying/packaging room. The warm air from the dryers meeting the damp of the eggs and conveying machinery creates a hot, humid environment with that could have the potential to be a breeding ground for bacteria if it weren’t for the ventilation system pulling in air from the rest of the plant, exhausting it here and filtering it before it comes back in. This same strategy is also utilized in the washing room. In addition to improving safety, it also makes for a more comfortable working environment.
Once dried, the eggs are tested for cracks with a hammer that taps on them. Eight microphones then listen to the frequency created by that tap to detect if there is a crack, the severity of the crack if there is and where on the egg that crack is located. Cracked eggs are removed from the process here. Those that pass the inspection go through one final UV disinfection process before continuing on to sorting and packaging.
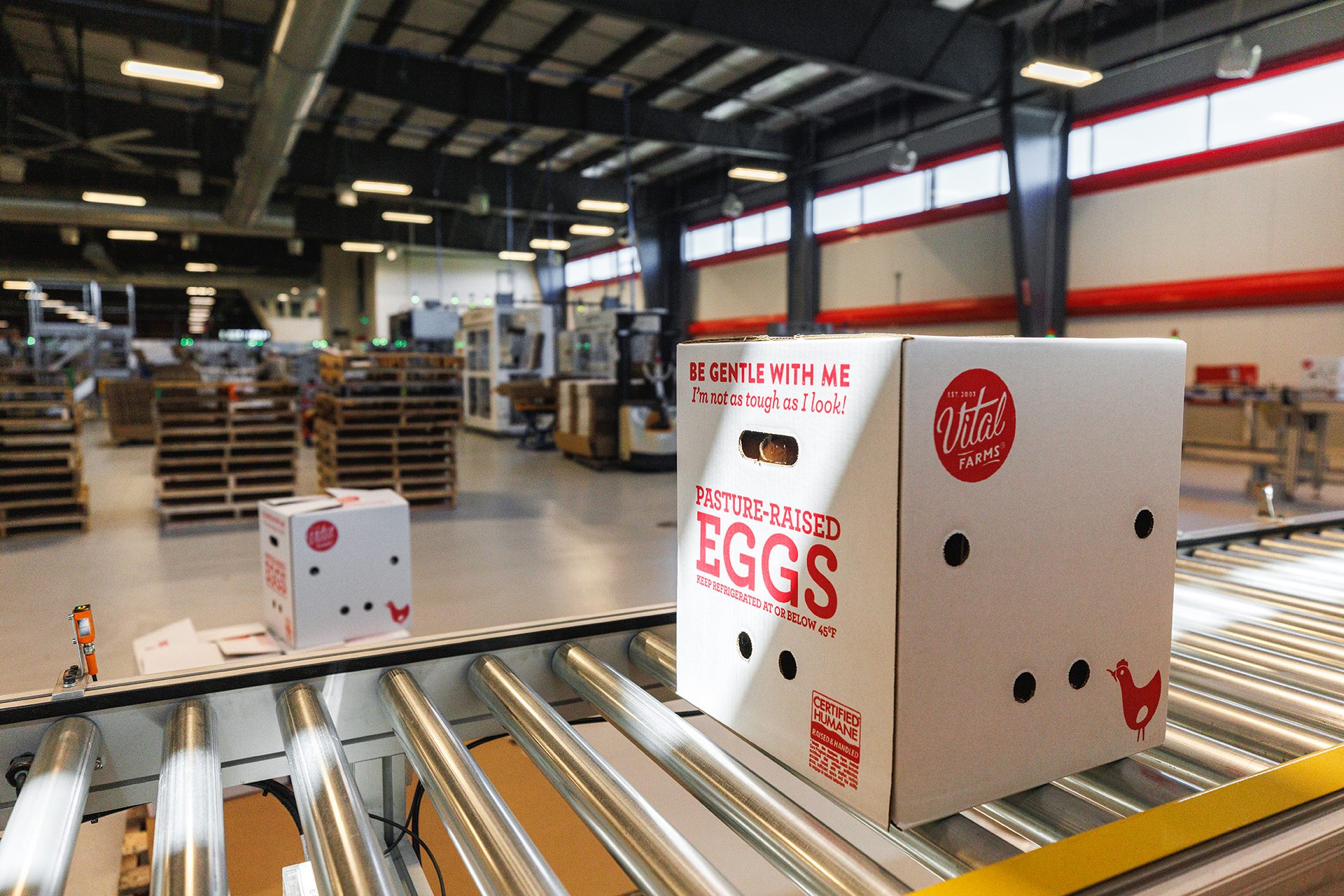
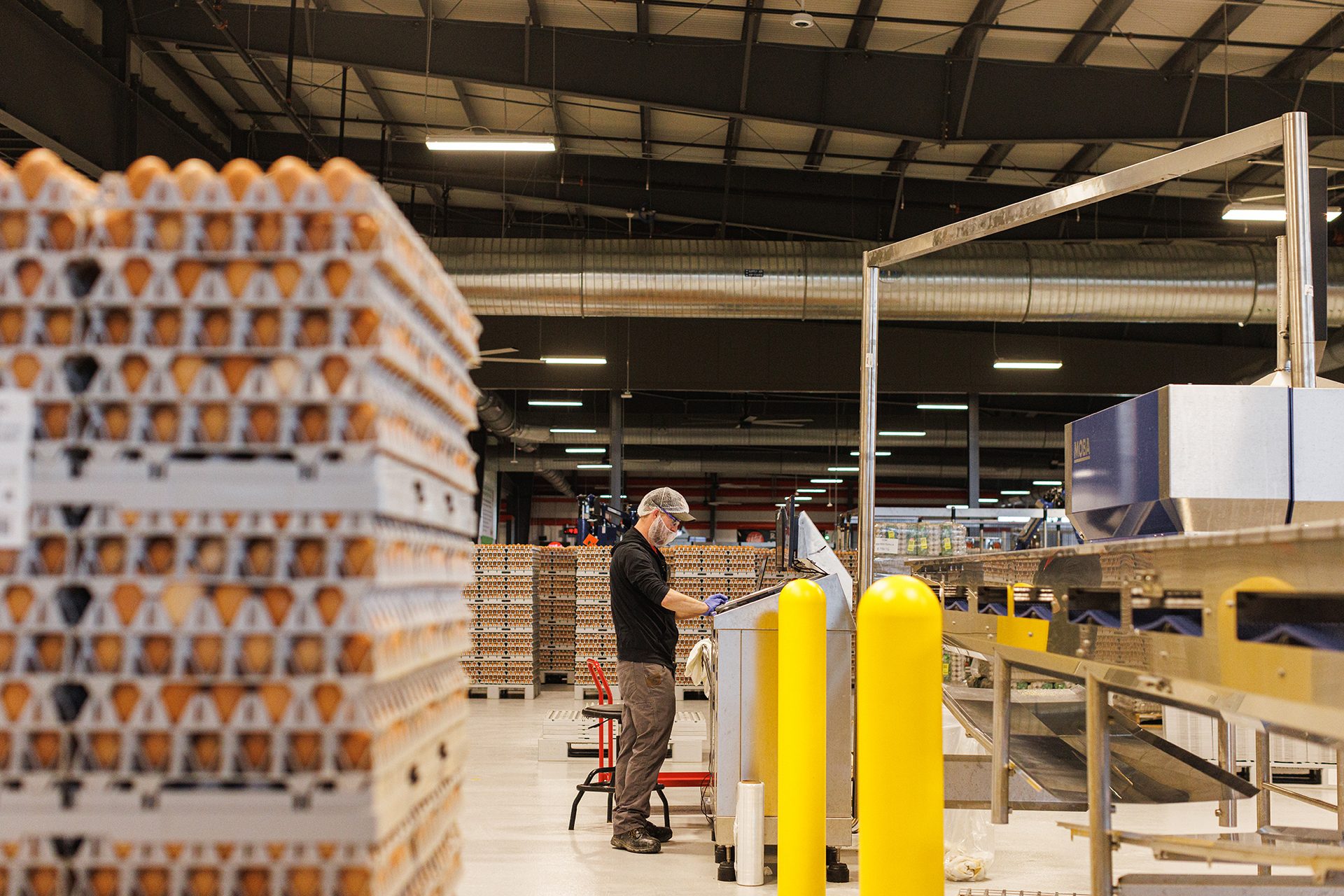
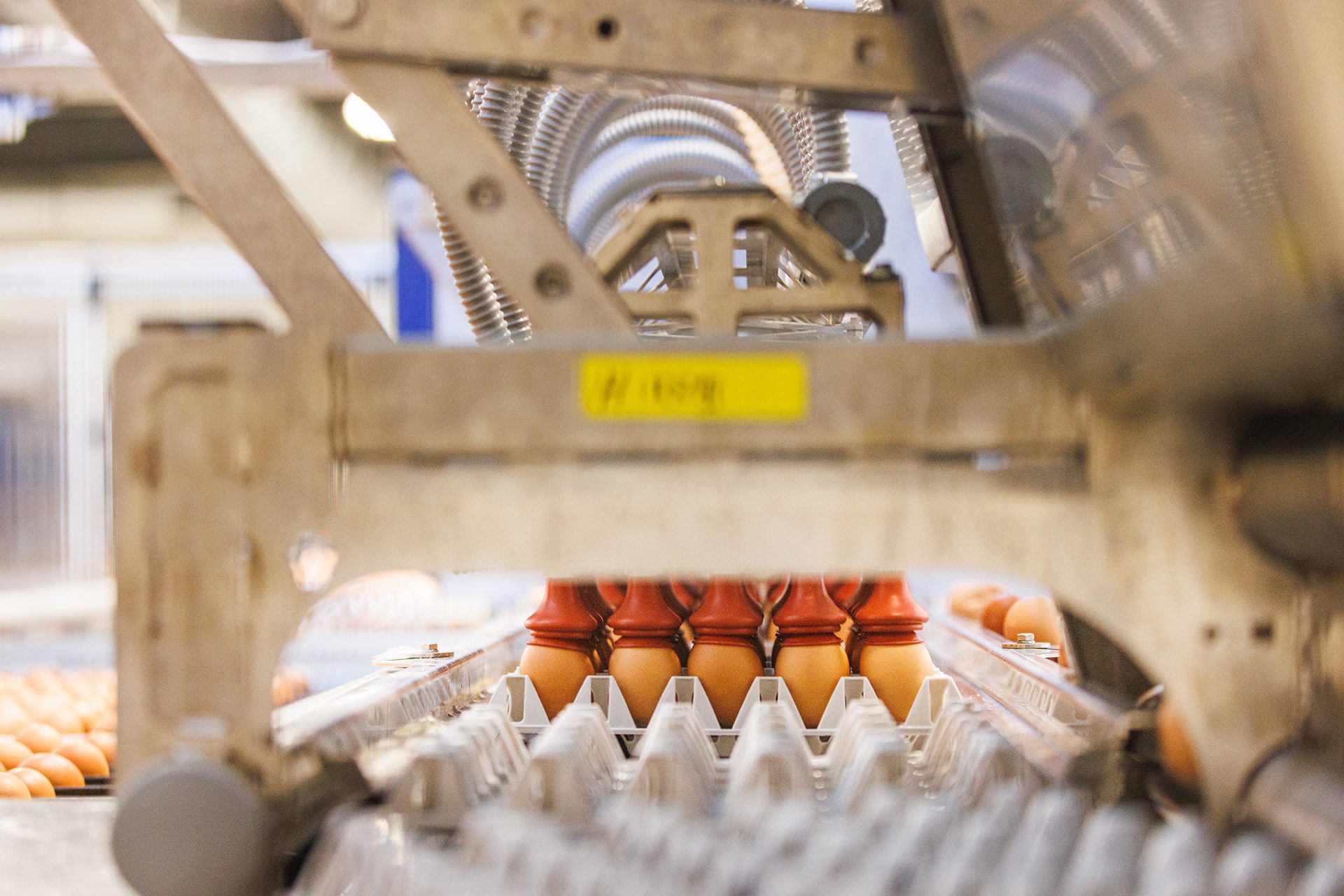
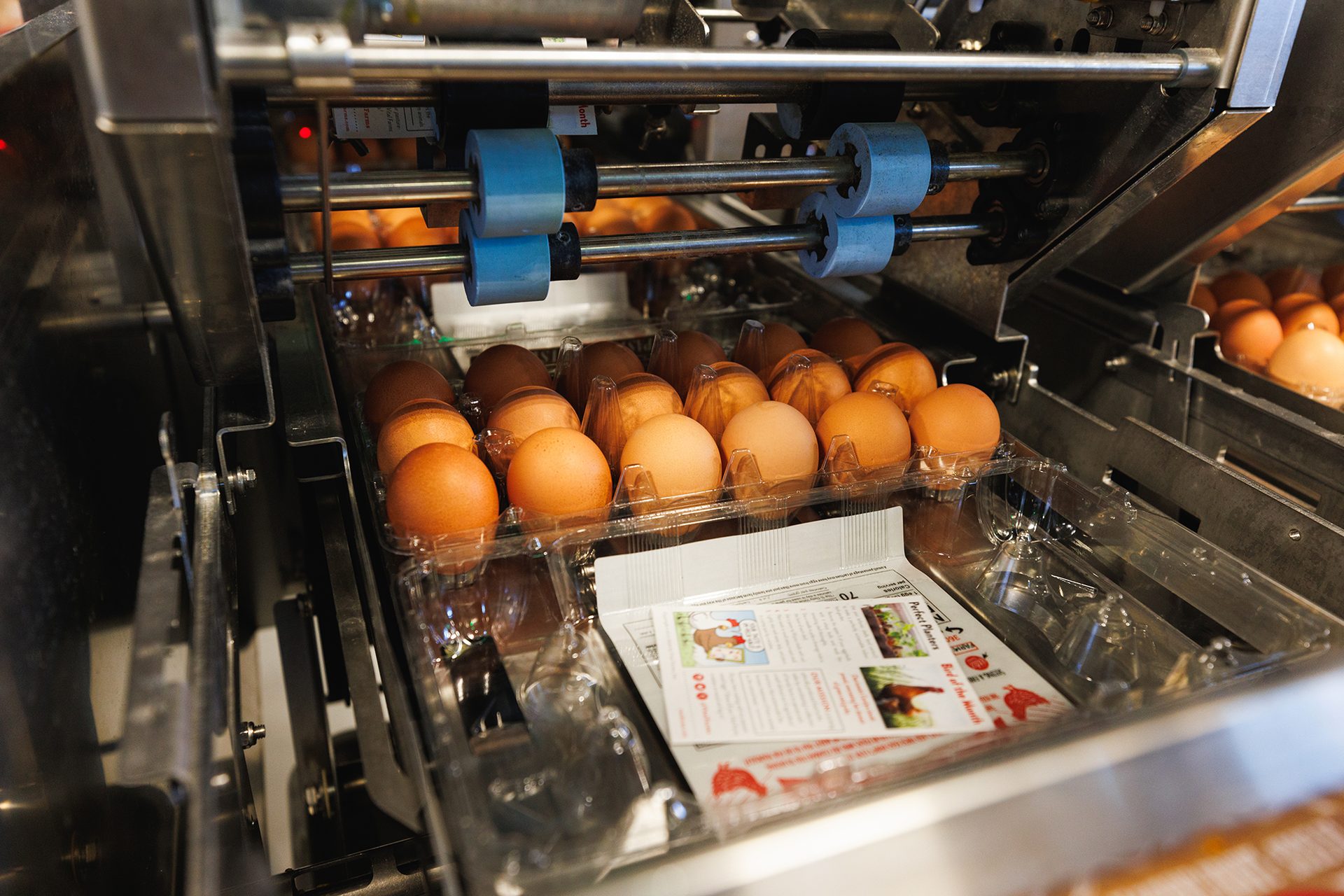
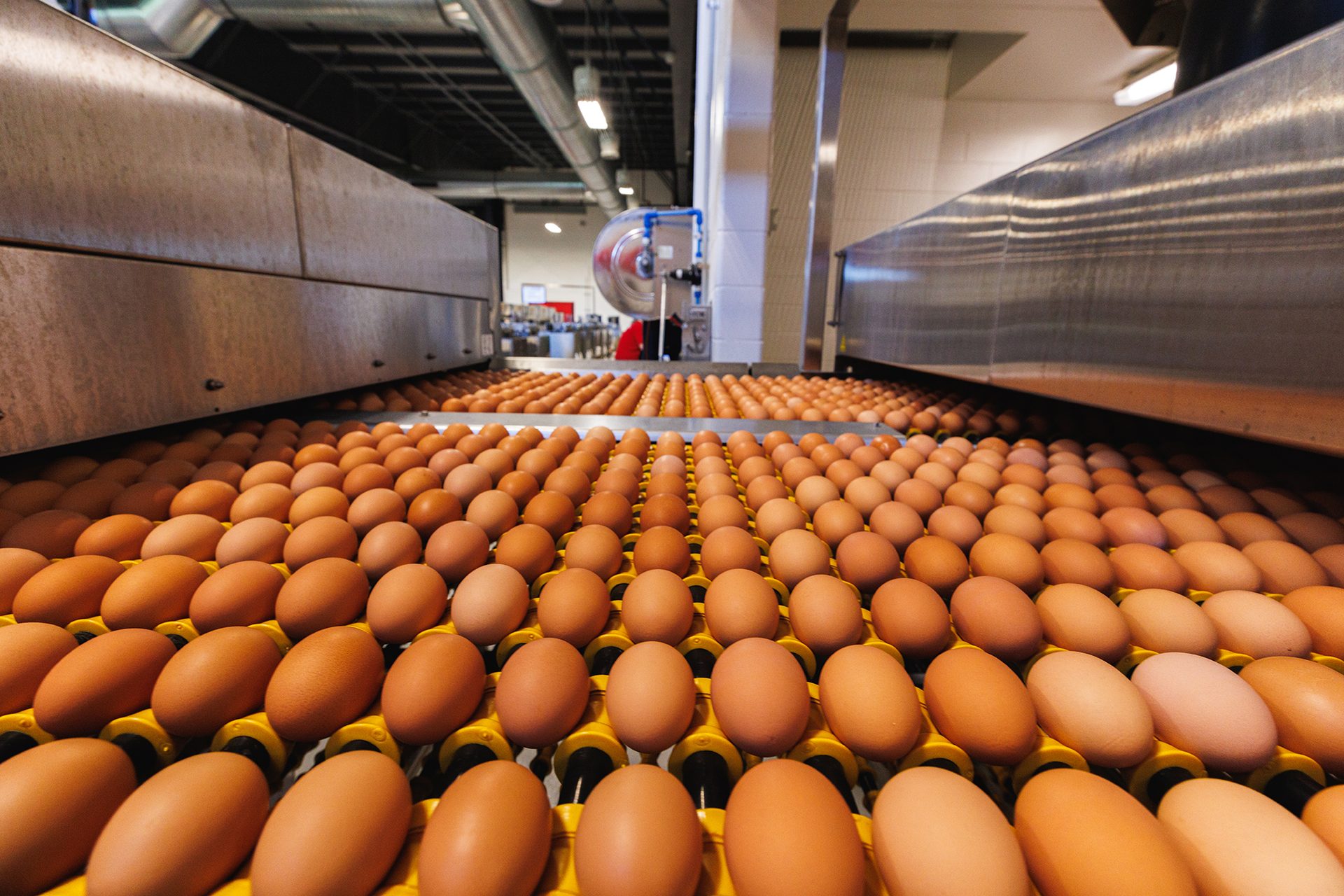
The processing goal for Egg Central Station is six million eggs per day. Despite that volume of production, it's still qualified for some of the highest standards of food safety.
The Shell and the Nest
While many of the decisions Vital Farms made to do with its site started with the original facility, the company is still finding room for improvement.
Preserving the site and minimizing the environmental disturbance to it were of the utmost importance. During the expansion, the company installed several retention ponds capable of handling several hundred thousand gallons of rainwater. These retention ponds capture rainwater discharged from the roof and parking lot where it’s filtered naturally before gradually being returned to local aquifers so as to prevent overwhelming the ground and creating drainage issues.
These retention ponds also serve to benefit the site’s “landscaping.” Instead of a carefully manicured lawn, Vital Farms has captured the beauty of the area by prioritizing indigenous species. Not only does this serve the local wildlife, it also benefits the company with a site in need of minimal maintenance and care.
“It's interesting: If you give the native landscape the right environment, it will naturally take over, hence why it's native,” says Kicklighter. “And so we actually spend more time removing the intrusive non-native, and then the rest basically takes care of itself.”
He adds, “During the summer it'll be full of wildflowers, and those aren't planted for us—that's what this area was before the building came here.”
More and more food production facilities are getting electricity through renewable sources. Cost tends to prohibit the installation of onsite renewable energy sources, which is why many turn to renewable energy programs offered by utility providers. However, Vital Farms went the extra step and recently completed installing solar panels above sections of its parking lot. The decision to put the panels in the parking lot as opposed to on the roof of ECS primarily had to do with how much the added weight could compromise the structural integrity of the roof. Additionally, the roof was designed to help reduce heat island effect, and installing the panels over the lot would help reduce the solar heat gain of the pavement, thereby reducing heat-island effect of the entire site. Employees appreciate the benefits offered by the panels, too—which keep the sun and rain from beating down on their vehicles during the summer and the snow from building up in the winter—making those spaces the most sought after.
Something to Cluck About
One of the most interesting facts about Vital Farms is that it doesn’t do much to tout itself and its endeavors or achievements. This is a Certified B Corporation that sends its eggs across the continental U.S. and has the most circulated newsletter in the country…if you count the insert that comes with each carton of its eggs as a newsletter. It continually works to improve the education and quality of life for its employees and surrounding communities through partnerships, sponsorships and learning opportunities. Many companies would be quick to issue a press release for any one of these, but not Vital Farms. This is why the company’s rationale for its pursuit of LEED Silver certification for Egg Central Station is so interesting.
Shades on the interior of the office space are adjusted automatically based on the time of day to be the most effective at shielding occupants from direct sunlight.
Retention ponds capture rainwater off of the roof and parking lot before filtering it gradually to nearby aquafers.
“The best way I would describe why we're doing it is recognition,” says Kicklighter. "That sounds a little egotistical or arrogant, but what I really mean is when we talk about recognition, there's a lot of hard work and thoughtfulness that was put into the facility. Recognition like that helps draw attention and gives us a bigger platform. Our voices are heard by more people and it helps us tell the story, so we get the recognition. But what that really does is gives us more ears to listen to what we're saying.
“And so we're able to tell the story of how you can be sustainable and still be a very profitable company and still create a good working environment and still put out a quality product,” he adds. “At the end of the day, we want more people to hear our story—and it's not in an arrogant or egotistical way. We think we can be a model for people to follow.” FE
Project Manager
Sandpebble Project Management
Speonk, N.Y.
http://www.sandpebble.com/
Architect
Buxton Kubik Dodd
Springfield, Mo.
http://www.buxtonkubikdodd.com/
Structural Engineer
Miller Engineering, P.C.
Springfield, Mo.
https://www.millerstructures.com/
Civil Engineer
Environmental Consulting & Technology, Inc.
Lombard, Ill.
https://www.ectinc.com/
Mechanical Engineer
Emtec Consulting Engineers, DPC
Ronkonkoma, N.Y.
https://www.emtec-engineers.com/about/
Energy Consultant
Entegrity
Fayetteville, Ark.
https://entegritypartners.com/
Project Team Members
JUNE 2023