march 2023
Automation
From Buzzwords to Real Needs
Automation Trends:
Automation will solve many problems—but not without people supporting it.
BY Wayne Labs, senior Contributing technical editor
Video courtesy of Getty Images / pidjoe
The food and beverage industry has been one of the slowest to adopt new technologies—and maybe that’s a good thing. The auto, chemical and petroleum industries, for example, have served well as testbeds for new automation technologies. Meanwhile, food and beverage has benefitted from all the trialing and proving of “bleeding-edge” systems such that the buzzwords we’ve used for the last few years—e.g., “digital transformation,” AI/ML, “digital twin” and Industry 4.0—are becoming everyday terms that describe technology we now rely upon to be competitive in today’s changing world of consumer tastes.
So, I asked system integrators, engineering houses and automation suppliers what their food processor clients perceive to be the three to five key trends/issues in automation today, and how processors are taking advantage of these automation trends. After tabulating the results, the top five trends cited were:
• Visualization (including enterprise, platform, machine and remote visibility)
• Data collection and analytics plus AI/ML
• Digital transformation
• Robotics and automated material handling (extending to warehouse automation)
• Security/cybersecurity.
Visualization Gets Processors through Blind Spots
Today, running a plant or two without visualization is a little like flying an aircraft on VFR (visual flight rules), which is just fine until you find yourself lost and disoriented in some unexpected weather conditions and you’re SOL. Flying on IFR (instrument flight rules) with instrumentation allows you to “see” what’s ahead when optical visibility is zero. Turn on the automatic pilot because it knows from sensor data which way is up or down or 70° to the right of your current course—even if you don’t.
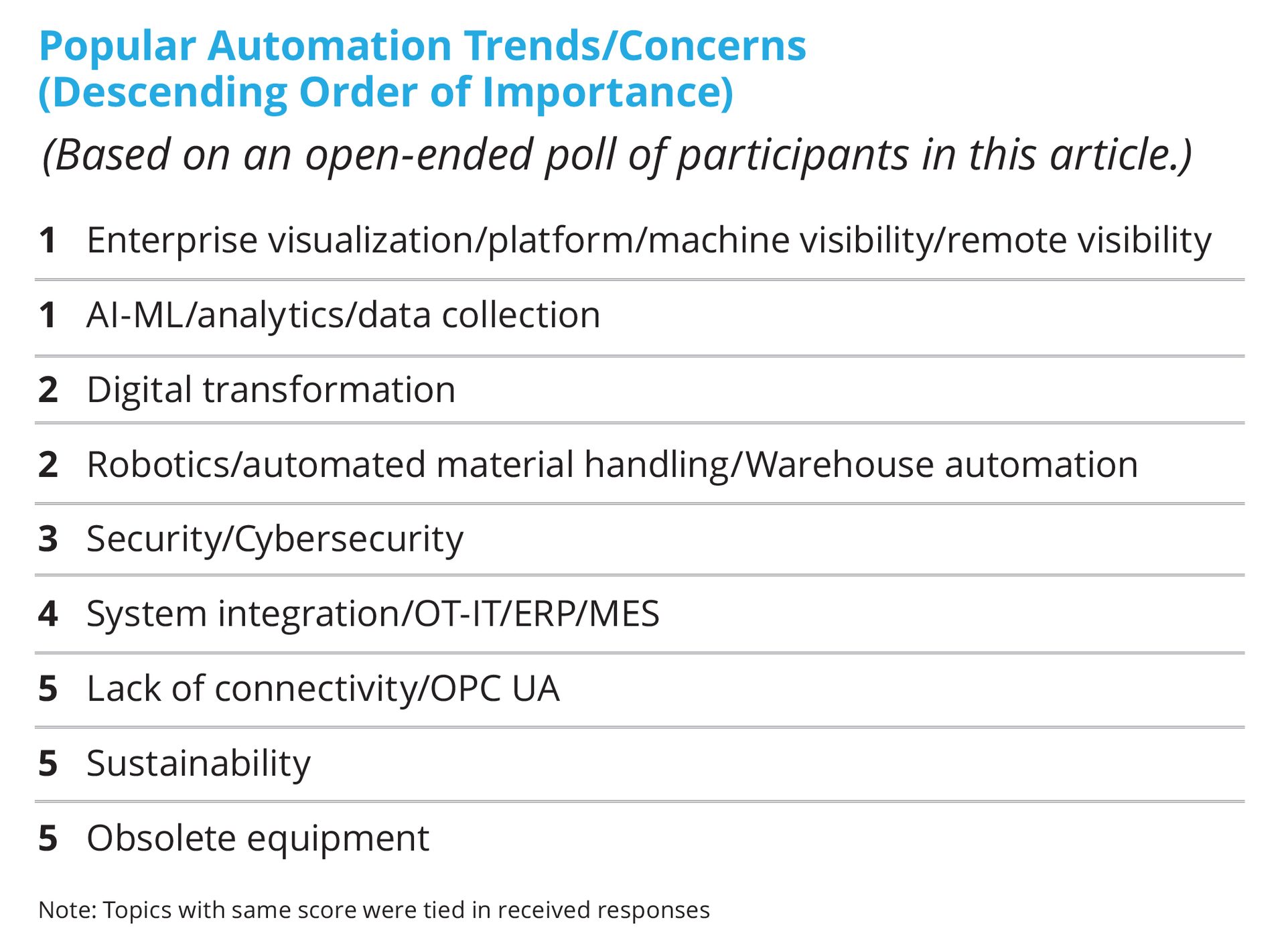
When I asked integrators and system suppliers what are the key trends affecting food and beverage processors, their most-often cited responses were enterprise visualization/machine visibility/remote visibility—and tied with visibility were the tools that provide the instrumentation food processors use to achieve the visibility; that is, analytics/data collection/AI/ML, etc. As in IFR flying, without sensor data to power the visualization/instrumentation system, you might as well be flying blind.
What drives the need for enterprise visualization? “The ability to monitor, harvest and analyze data allows manufacturers to be more responsive to a marketplace that demands flexibility while dealing with supply chain and lean manufacturing issues,” says Dean Elkins, Sr., director, advanced automation at Gray Solutions, a Gray Company.

Today’s vision systems not only inspect food, but also barcodes and date codes as well, making this data available to track-and-trace and production systems. Photo courtesy of Grantek
Indeed, processors are wanting more digital trending, system monitoring—and user monitoring in their systems, says Josh Nichols, Dennis Group engineer. “They want to see historical trends, custom batch reports and track user changes.” And to make enterprise visualization possible, processors also want remote access, integration of enterprise level systems with industrial-level systems and all the security needed to make network visibility possible, adds Nichols.
Visualization at the enterprise level is also being driven by common business tools, for example from Microsoft—like Office 365 and Power BI (Business Intelligence). “Power BI is driving a significant increase in enterprise visualization,” says David McKenna, director of smart manufacturing solutions, Grantek, a Control System Integrators Association (CSIA) Certified Member. “This is in the early stages, but when combined with digital transformation, adds real value. In my opinion, some enterprise visualization offerings may just be old SCADA, but companies like Inductive Automation with their innovative licensing model and software support deliver valuable features. The buzz about Industry 4.0 in general has provided a very positive boost to traditional SCADA work, as well as more innovative bridges to ERP, etc.”
AI/ML tools, as we’ll see later, add more visibility to plants and processes, but augmented reality (AR) overlays the physical world with descriptive and prescriptive information, which answer the questions, “What am I looking at?” and “What should I do with this?” These tools are desperately needed to supercharge the onboarding of new employees in manufacturing roles and boost productivity of current employees, says Lachlan Stokes, transformation partner at Rockwell Automation. Another good application for AR is maintenance, where the overlay of video and actual machine aids maintenance workers in locating and quickly fixing the problems.
Snags in Achieving Visibility
While there’s no question visualization at any level will help processors get a handle on their process, many older facilities suffer from two problems caused by their age: lack of connectivity and obsolete equipment.
“The first thing we’ve seen from our food and beverage accounts is a drive to connect the assets,” says Matt Ruth, president of Avanceon, a CSIA Certified Member. “Meaning, connect the assets to Ethernet and subsequently to the overall operational technology (OT) network with the expressed purpose to ensure that they can get access to the OT equipment to influence and extract information. This connection means that manufacturers will have an insight into the machine itself and not have to guess at its status. After this connection is in place, the food and beverage manufacturer is able to make better decisions based on the exposed insight. The challenge is that, in many cases, the connection is not viable because the machine is operating using obsolete control systems.”
That brings us to the second stumbling block in attaining the connectivity needed, says Ruth. “Obsolete equipment is a challenge for manufacturers because it is not straightforward to gather the information they need to drive improvement. It has also become next to impossible to procure replacement parts in the event of critical failure. Obsolescence and upgrade efforts are a commitment to make everything have a serviceable and connectable level of software, hardware, and firmware.”
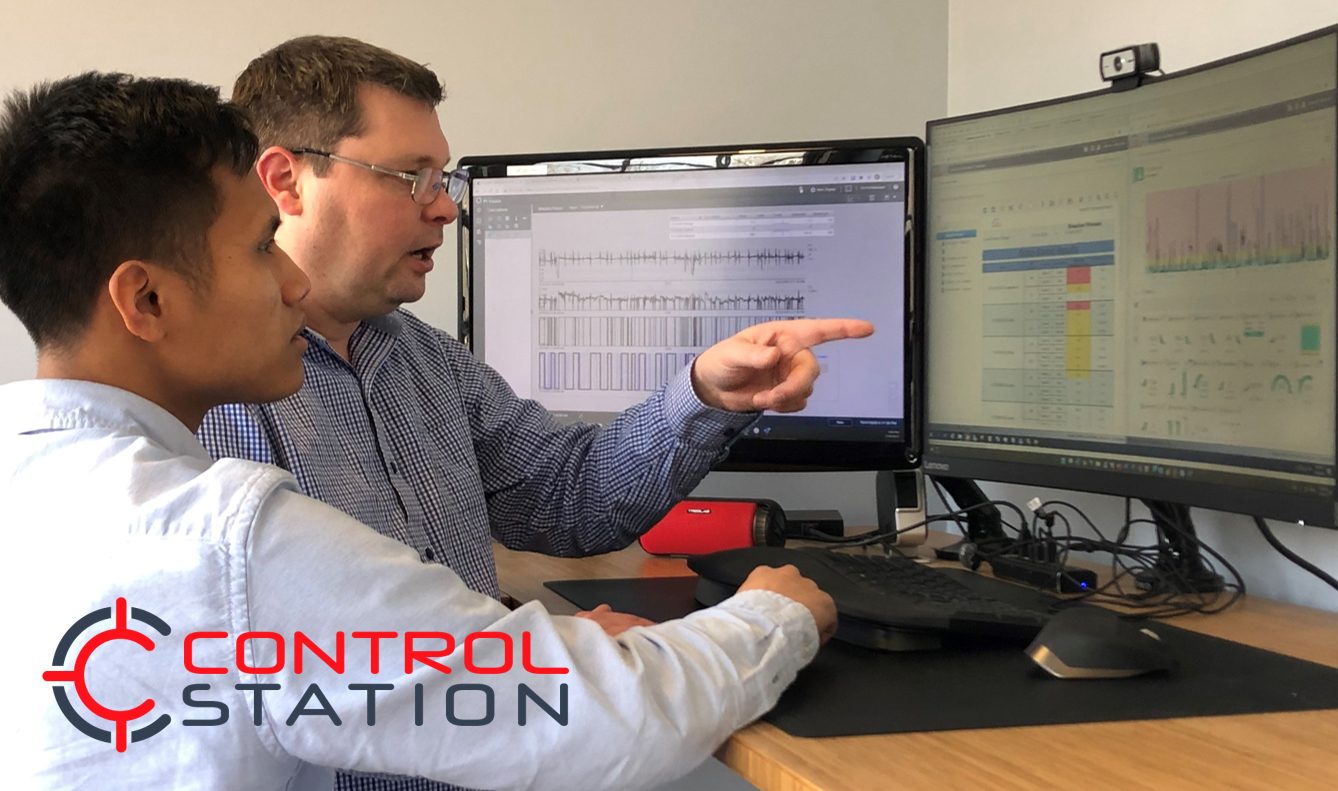
Control Station PlantESP software lets food and beverage users easily and securely access and analyze process data spanning multiple units and sites, so they can discover and act on non-obvious opportunities to achieve greater operational optimization and savings. Photo courtesy of Control Station
With the right connections, food processors can have remote access when needed, and with IT and OT talking to each other such that the ERP is tied into production systems, manufacturers can plan production schedules with actual data, says Nichols. However, he warns that security is an integral part of the system. “When combining IT and OT networks, security should always be a topic of concern. Ensuring the correct people and applications have access to the data they need without leaving company vulnerable to cyber intrusion should be top priority in any networking project.”
AI/ML, Analytics and Data Collection
Tied for first place mentions in the survey was AI/ML/analytics/data collection. Data collection isn’t a new concept, and it goes back to the historians in the early 1990s. The quest to see what’s going on in an enterprise is placing new demands on data collection as we know it.
It’s time for new tools, says Bob Rice, Ph.D., vice president engineering, Control Station Inc. “The age-old race continues for manufacturers to gain a competitive advantage by increasing throughput and reducing costs. If viewed through a Six Sigma lens, then it becomes clear that most of the industry’s potential gains have been realized using traditional tools—the low hanging fruit has already been picked. Now those in the food and beverage industry are adopting a new set of analytical tools that promise to uncover non-obvious opportunities for optimization. Those tools require data to be served up from numerous individual production facilities so it can be accessed and analyzed centrally.”
“With economic downturn, the need to analyze and optimize existing facilities is important,” says Roger Kredit, lead control systems developer at CRB. The focus is to be able to provide automation to self-tune using artificial intelligence (AI) to increase efficiencies of production. If AI isn’t available, providing the ability to capture and visualize is essential to KPI information. Automation helps engineers and subject matter experts realize and address issues.
For many food and beverage organizations there has been an increase in demand, and they are forced to increase automation to be able to keep up, says Marcel Koks, Infor senior director, industry & solution strategy, food & beverage. Other drivers for automation are lack of raw materials and increased focus on food safety, says Koks. “These drivers have triggered new ways of thinking, e.g., use of AI & ML for yield optimization and computer vision systems for grading and identifying optimal ways of processing. Not only are these initiatives increasing efficiency but are also resulting in more consistent quality and with less waste.”
AI can play practical roles in a line, according to Derrick Colyer, business development manager and automation engineer, E-Technologies Group, CSIA Certified Member. “A good example is using AI in filling technology—specifically the predictability of bottle filling. For example, a label says 16.9 fluid ounces on the bottle, and if you were to fill it any less you would be falsely advertising your volume. Oftentimes producers will over fill 16.9 ounces, which of course the consumer doesn’t care about because they’re getting more product for free. The producer, however, could be losing a lot of profit. AI can answer the question: How do I get an exact amount of fluid and get paid for the exact amount of product I’m putting out there? How is the maintenance of my mechanical hardware effecting the fill volume? When is the right time to perform that maintenance? How can I adjust PID parameters based on mechanical usage, changing weather patterns or changes in fluid dynamics?”
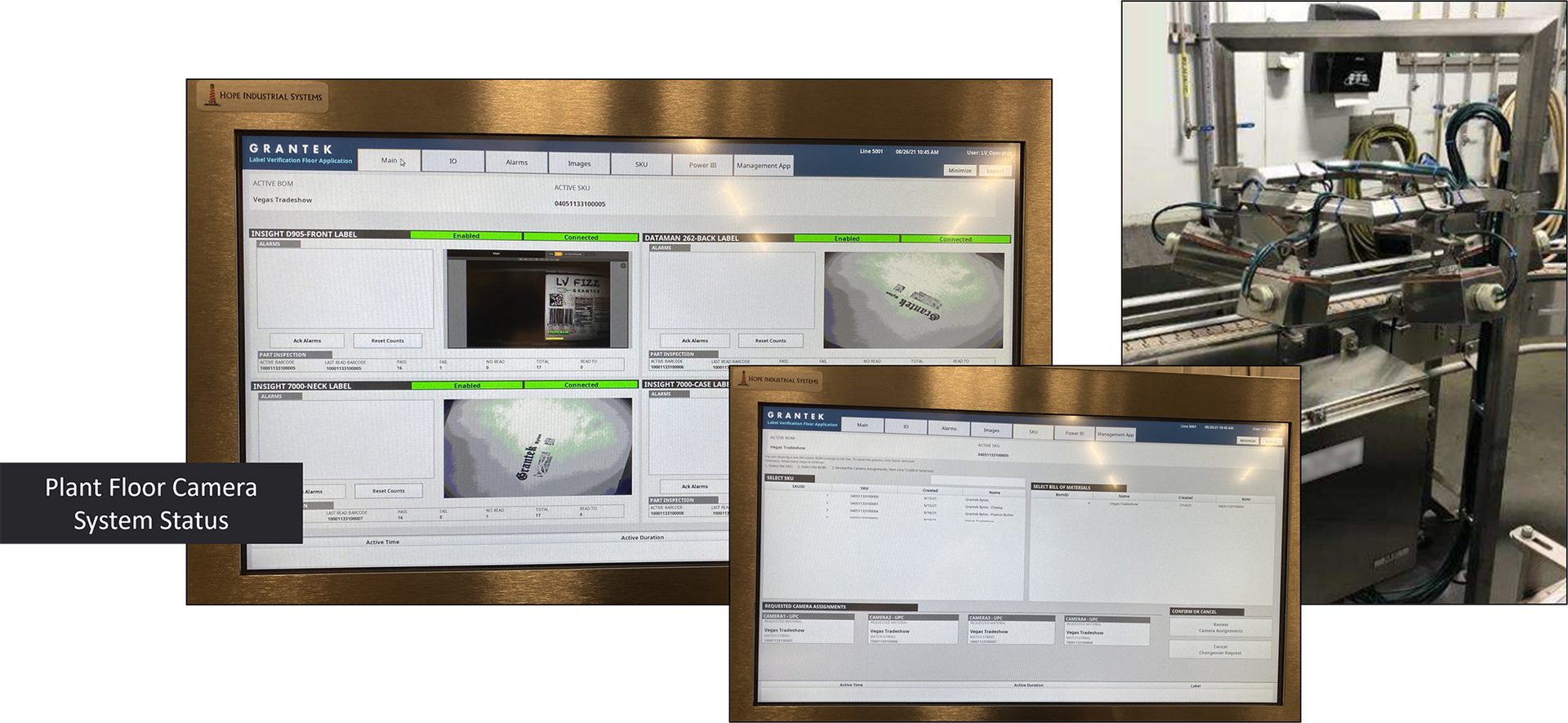
Grantek provides a complete solution for label verification, making track and trace easier throughout the plant. The system verifies 1D or 2D barcodes from IPC to Data Matrix to Code 128—and also inspects date codes and checks for product defects. The system uses industry standard PLC, HMI and vision hardware and can be customized for various modes of line operation. Photo courtesy of Grantech.
Another good AI application revolves around processing cocoa beans, says Mary Anne Ballouz, ICONICS marketing. Cocoa powder production, where the key ingredient (cocoa beans) exhibits a high variation in quality, results in batches that are extremely difficult to blend perfectly every time. Prescriptive AI can be used to guide operators to blend the ingredients in such a way that they are able to meet the specifications of that batch in a drastically reduced amount of time.
Digital Transformation: What Does it Really Mean?
The term, “digital transformation,” which was tied for second place in our survey, seems an overworked term that has lost some of its meaning—suffice to say it can probably serve as a wrapper for everything covered in this article. After all, isn’t this what we seek when we have applied technology to a facility and its methods, process and operation?
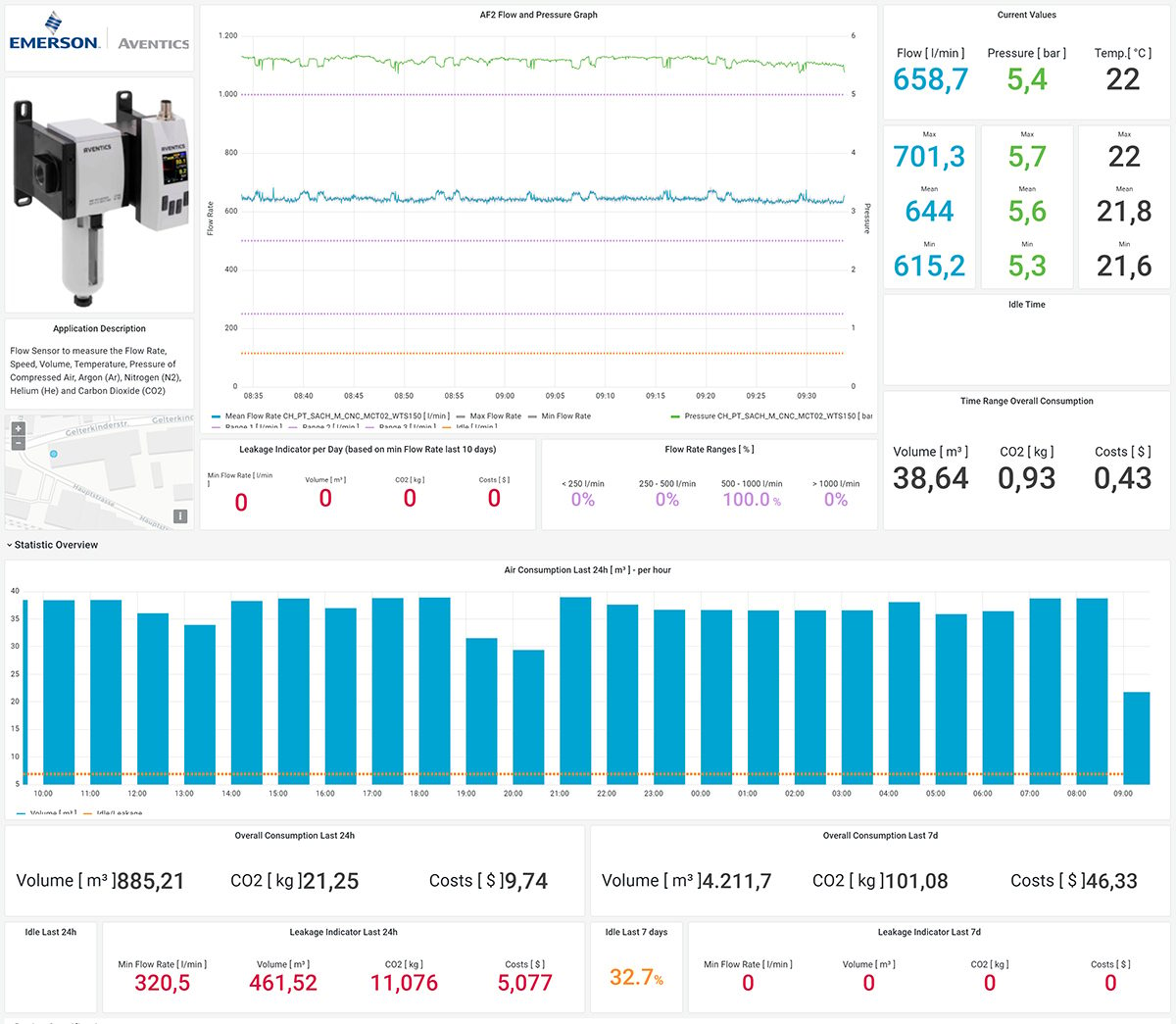
Emerson digital transformation and edge technologies, delivered through a fully coordinated portfolio of hardware and software, are helping food and beverage end users and OEMs with the automation and analytics needed to achieve their goals for machine optimization and sustainability. Graphic courtesy of Emerson
Digital transformation must happen before a company can consider things like AI, wireless tools, lack of connectivity, etc., says Colyer. “Digital transformation must be planned for and also must be included in your operations plans for your personnel, too. A successful digital transformation enables the right data to get to the right person at the right time! And then, the person must be equipped to utilize that data for the benefit of the organization.”
However, as catchy as the term is, digital transformation is easier said than done. “Industry is racing toward digital transformation, having invested significant effort and treasure in both infrastructure and analytics,” says Rice. “However, integration of the various systems and applications represents a major hurdle for virtually all manufacturers, especially those who are pursuing digital transformation at an enterprise level. It’s not that manufacturers don’t have access to the right tools, it’s that many of those tools continue to operate in separate silos which hampers a manufacturer’s ability to extract maximum value. But caught in between is data security. This is a known challenge that will only become more complex as cyber threats continue to rise and put enterprises at risk.”
OEMs are placing a top priority on applying increased automation and digital transformation to satisfy their customers’ key focus areas of sustainability and continuous process automation and improvement, says Ajay Rana, industry marketing leader-food & beverage, life science, CPG, Emerson. Edge-driven technology—applied to CIP systems for example—upgrades manual processes to more effective automatic operation and provides the reporting and dashboards needed for users to improve overall equipment effectiveness, utility usage and other optimizations. The same concepts apply to many other types of equipment and processes.
Nevertheless, digital transformation provides solutions to aid with transparency of an organization’s ESG footprint. For example, waste production, energy consumption and safe and ethically sourced ingredients are a focus in every board room, says Rockwell’s Stokes. “We recently partnered with a producer of infant formula and one of our supply chain software partners to provide end-to-end unit-level serialization and traceability that greatly enhanced brand integrity and consumer confidence, which not only accomplished the regulatory compliance objectives but provided them a differentiated competitive advantage at the retail point of sale,” says Stokes. Energy management software, water quality and leak detection applications as well as traceability across a product’s value chain will be a top priority for food and beverage organizations for years to come, adds Stokes.
Robotics and Automated Material Handling
According to an ARK INVEST research study updated in 2019, the cost of an industrial robot in 1995 was $133,382 in 2017 dollars. The study projects that the same robot will cost less than $11,000 per unit in 2025. Combined with advances in machine learning and computer vision, robot unit sales are projected at 3.4 million, up roughly 380,000 recorded in 2017.
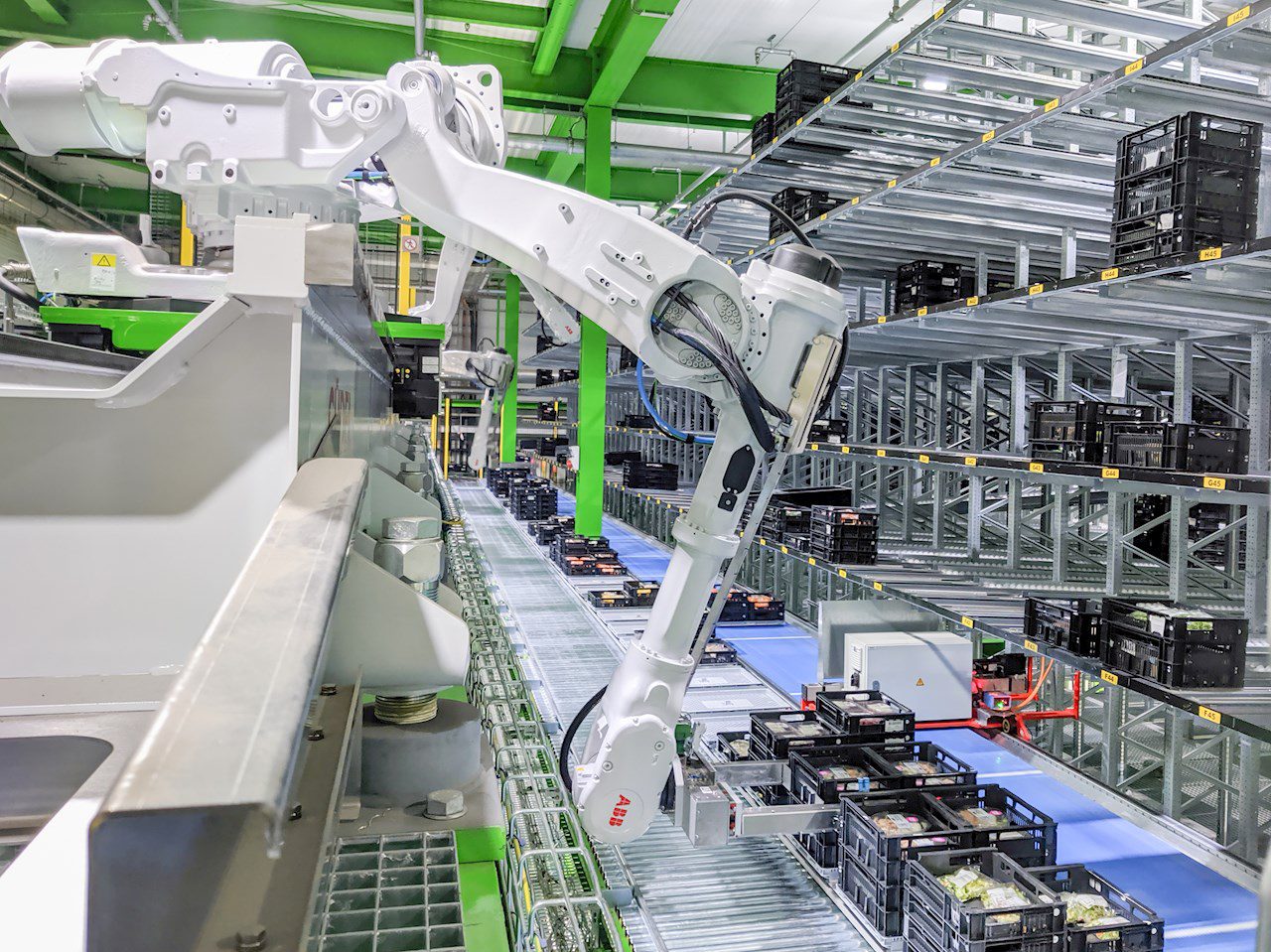
ABB supplied a robot-centric solution to automate the order picking operations at Heemskerk’s grocery sorting production facility. At the beginning of the product flow is an ABB IRB 660 four-axis robot that removes crates containing the orders for a particular supermarket and places them on a conveyor belt. Photo courtesy of ABB Robotics
In our survey of interviewees, robotics and automated material handling ranked second, tied with digital transformation. Robotic automation has recently been providing food manufacturers the infrastructure that provides the flexibility to handle a wide variety of goods in the widest range of combinations and in the shortest possible time, says Ali Raja, vice president – consumer market segments, ABB Robotics.
The three most pressing trends in automation are designed to meet the challenges of today’s economy, says CRB’s Kredit. The first is to use automation—like autonomous solutions and robots—to supplement or offset employee shortages. Automation simplifies processes and takes on basic tasks to help cover gaps where finding employees is hard.
The Dutch fresh foods company sought a flexible and scalable automation solution to pick and stack orders, and deliver the freshest food, just in time to supermarkets and other food service companies. Robotics, says ABB’s Raja, solved several problems. The system addresses minimal waste, fresh food/longer shelf life, custom orders/flexibility and direct-to-retailer delivery.
Westvlees, Belgium’s largest pork producer, installed ABB robots as part of a just-in-time order fulfilment system that delivers customized products to supermarkets more quickly. The system addresses just-in-time order fulfillment, reduced lead times, increased shelf life, direct-to-retailer delivery and custom orders/flexibility, says Raja.
A challenge in the past, the process for chicken and meat deboning assisted by vision and scanners now allows processors to get much closer to the bone, which creates far less waste. The greater availability of more hygienic and easier-to-clean robots has also created a more sterile environment for the deboning processes and can work in the higher temperatures that are ideal for deboning. In addition to enhancing the process, robotic automation in this application improves both the quality and shelf-life of the chicken, says Raja.
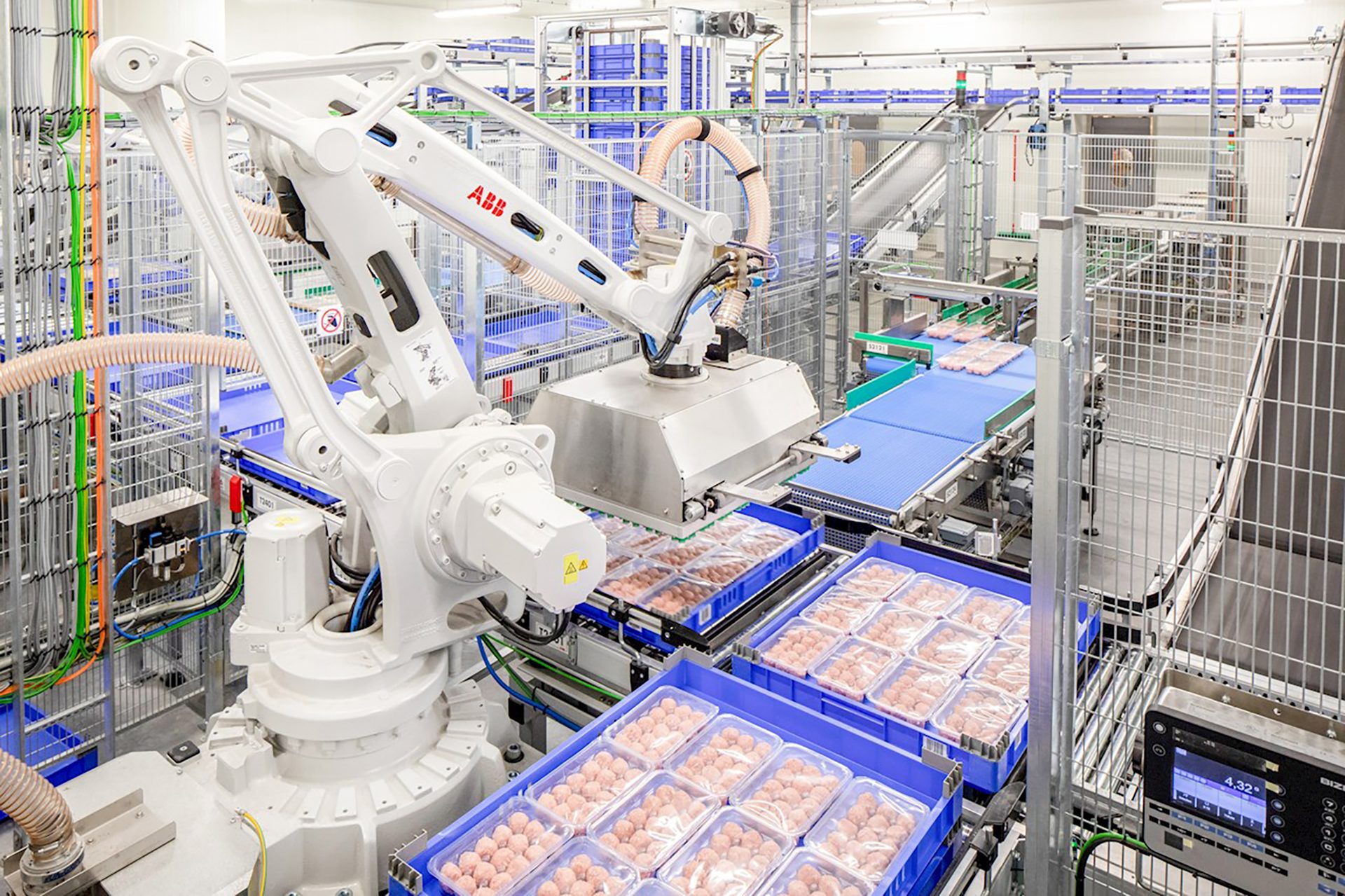
Belgian meat products company Westvlees NV has built an order fulfilment center that has increased the shelf life of products by 20% and reduced the lead time from order to delivery by 50%. Delivered to the supermarket chain’s stores, the prepacked pork products are individually labelled for each shop, cutting the time needed to get products onto the shelf. Photo courtesy of ABB Robotics
Security/Cybersecurity
Security/cybersecurity came in at number three in our open-ended poll. Security is driven by both regulatory needs and increasing visibility of vulnerabilities in system and networks. Security issues can impact IP, product safety and worker safety, making these areas mission critical, says Alan Stanfill, director, digital transformation at Gray Solutions, a Gray Company.
“Of the trends I’ve been keeping an eye on recently, the most important is cybersecurity,” says Raymond Berning, automation manager at Interstates, a CSIA Certified Member. “Cyber threats are continuously increasing, and food processors are understandably concerned about keeping their facilities safe and protecting quality control.”
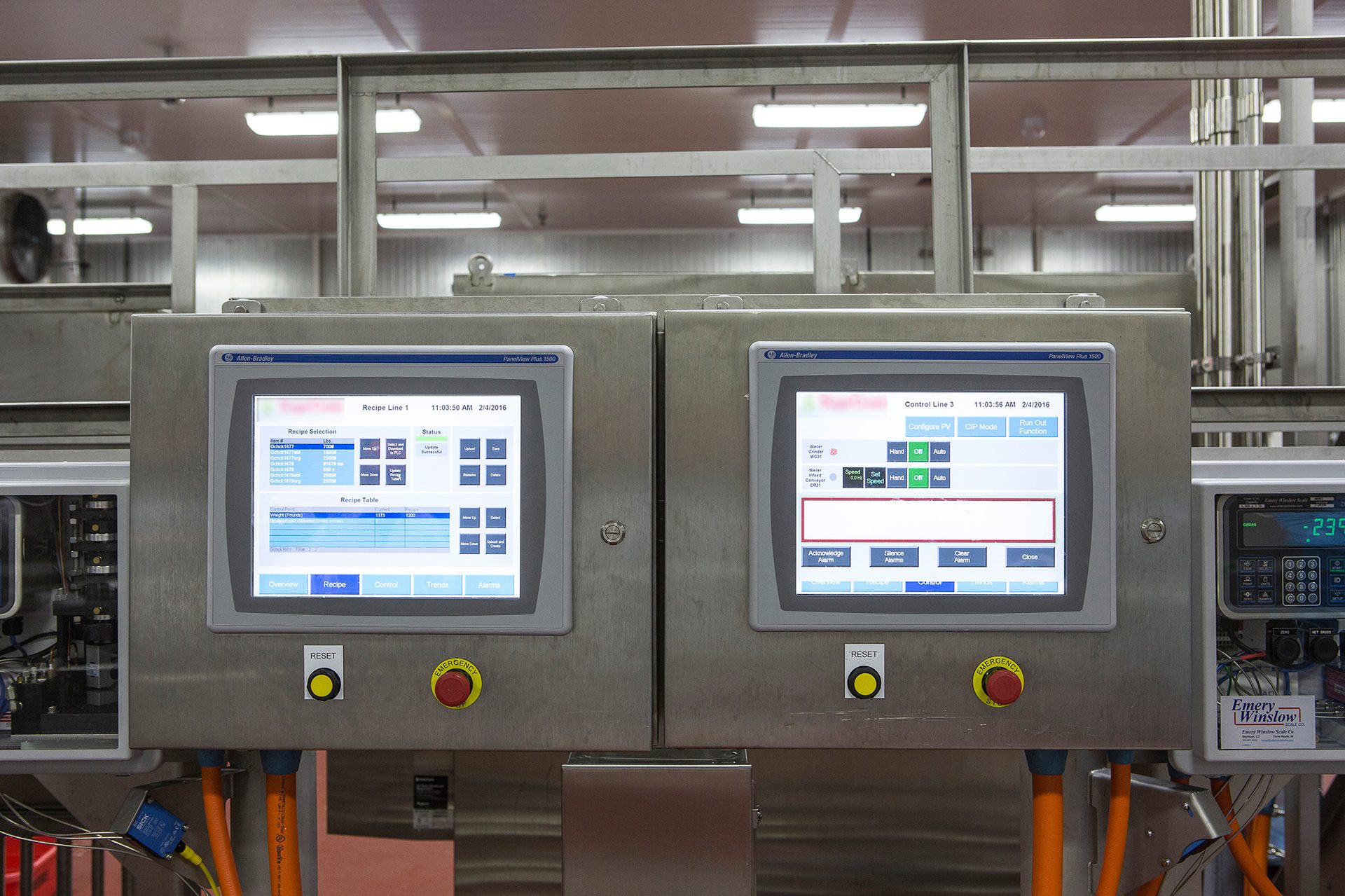
In a modern automated system, data and sometimes the control functions as well are made available via wireless devices such as tablets and phones. Photo courtesy of Ross Van Pelt, RVP Photography
No one is exempt from a cyberattack, says ICONICS’ Ballouz. “Cyber criminals are targeting food and beverage organizations—and not just large organizations but also smaller ones—especially their supply chains. Organizations are using automation to gain the visibility needed to ensure that those connected to their networks are not a liability, particularly since personnel use tablets and other mobile devices on the manufacturing floor which can be potential weak points in security.”
“The main drivers behind cybersecurity and analytics trends in our industry are food safety and demand,” says Berning. “Your goal is to ensure nothing can act to shut down your facility or contaminate your product. When you must shut down for a week or more for cleaning or have to run at reduced capacity while you retool your line, it directly impacts consumers. We all saw what happened with prices and availability at the grocery store during the pandemic. Seeing empty shelves left and right was a stark reminder of what’s at stake.”
Challenges Remain
“I’d argue that security is and will continue to be the biggest challenge facing the food and beverage industry for the foreseeable future,” says Control Station’s Rice. “It is challenging to balance the openness of data that drives analytics and the protection of network infrastructure that prevents intrusion. It seems that perpetrators of cybercrimes are ahead of most IT teams, using advanced network penetration strategies as well as tried-and-true malware. With the launch of each enterprise IT networking and/or application integration project, manufacturers will be increasingly at risk of cyber threats from bad actors.”
While end users and OEMs know they need to undertake digitalization to remain competitive, it can be challenging to know which newer technologies to adopt, over and above reliable and traditional automation practices, says Emerson’s Rana. Many large top-down digitalization efforts have failed to return value, and implementers are rightfully concerned about going down the wrong path by investigating and pursuing technologies that will not scale up, are difficult to support or may not provide adequate cybersecurity. FE
MARCH 2023