Cleaning part 2
Changing Consumer Attitudes on Sustainability
There are several cleaning and sanitation methods — each with their own unique capabilities. Combining methods with a plan in place can help ensure that products are safe and the facility and its equipment are free of foodborne bacteria.
Fighting the Foodborne Bacteria War with
Cleaning and Sanitation
About Dry Cleaning: Superheated Steam, Chlorine Dioxide and UV-C Light
Dry steam cleaning utilizes steam with minimal moisture content, making it suitable for sanitizing equipment in both high-moisture environments, such as meat production, and low-moisture facilities, such as bakeries, says Novolyze’s Khinouche. Its advantages include effective microbial reduction and the ability to reach intricate areas without excessive water use. However, its efficacy in physically removing biofilms and heavy residues may be limited, necessitating mechanical action or chemical interventions. Operators should use appropriate personal protective equipment (PPE) to prevent burns or injuries.
“Steam cleaning can be used in specific applications, generally where there is a relatively low level of soil to be removed and where the use of water is not welcomed, as it may affect the production or the product food safety,” says Diversey’s Tardioli.
“We need to consider that to clean is to dissolve a soil and displace it from the surface to the drain (or anywhere the specific case requires),” Tardioli adds. “Wet cleaning makes use of chemicals to saponify, oxidize and physically break the bonds of contamination so it can be resolubilized in water and washed down the drain. Steam can effectively act on some soils, but we still need to displace it somewhere, and this is not always practical, safe for the operators or financially attractive to be performed in greater scale across all applications. So, this can indeed be used in specific applications where water needs to be heavily controlled and limited, but at the moment, it cannot replace traditional wet cleaning solutions in many key industries, such as meat, poultry or fish, where the majority of soils require water-based chemistries.”
Steam cleaning is not 100% “dry” because it involves steam, says Ecolab’s Walsh. But this is true of many solutions that typically fall under the dry-cleaning umbrella — they aren’t completely free of moisture, but they are specially designed to reduce the need for water in the C&S processes as much as possible. One of the major innovations in the dry-cleaning space is the development of fast-drying sanitizers.
One solution worth mentioning for its effective use against pathogenic contaminants is chlorine dioxide — a powerful antimicrobial registered with the EPA as a sterilant, says Ecolab’s Herdt. Chlorine dioxide is useful for hard-to-clean equipment, dry-cleaning environments and spaces where liquid microbials can’t quite reach. Because of its molecular size and status as a true gas, chlorine dioxide can penetrate areas where microorganisms are hiding and can’t physically be reached. And because it is a gas, it leaves no residue behind, eliminating the need for a post-clean rinse and further supporting moisture reduction.
These properties make chlorine dioxide a highly thorough and flexible option for a number of different applications. Manufacturers can target specific pieces of equipment by tarping them and creating a sealed environment, or they can isolate a product pathway within the equipment itself. They can also scale the treatment to treat a space of much larger size. Of course, chlorine dioxide treatments must be applied under very controlled conditions to prevent workers from being exposed to the gas. Typically, this involves a partial or full shutdown of the facility, with production downtime ranging anywhere from a few to several hours, depending on the amount of space being treated, Herdt says.
Photo courtesy: Novolyze
By Wayne Labs
UV-C light is effective for surface sterilization of equipment, particularly in low-moisture environments where traditional wet-cleaning methods are impractical, says Novolyze’s Khinouche. Its practicality depends on factors such as line-of-sight exposure and material compatibility. Typically, UV-C is applied after processing has concluded to avoid potential hazards to personnel and product degradation. It can be used on empty conveyor belts; however, ensuring uniform exposure is crucial. In some cases, dry steam cleaning may be preferable for its ability to remove residues physically, depending on the specific sanitation requirements.
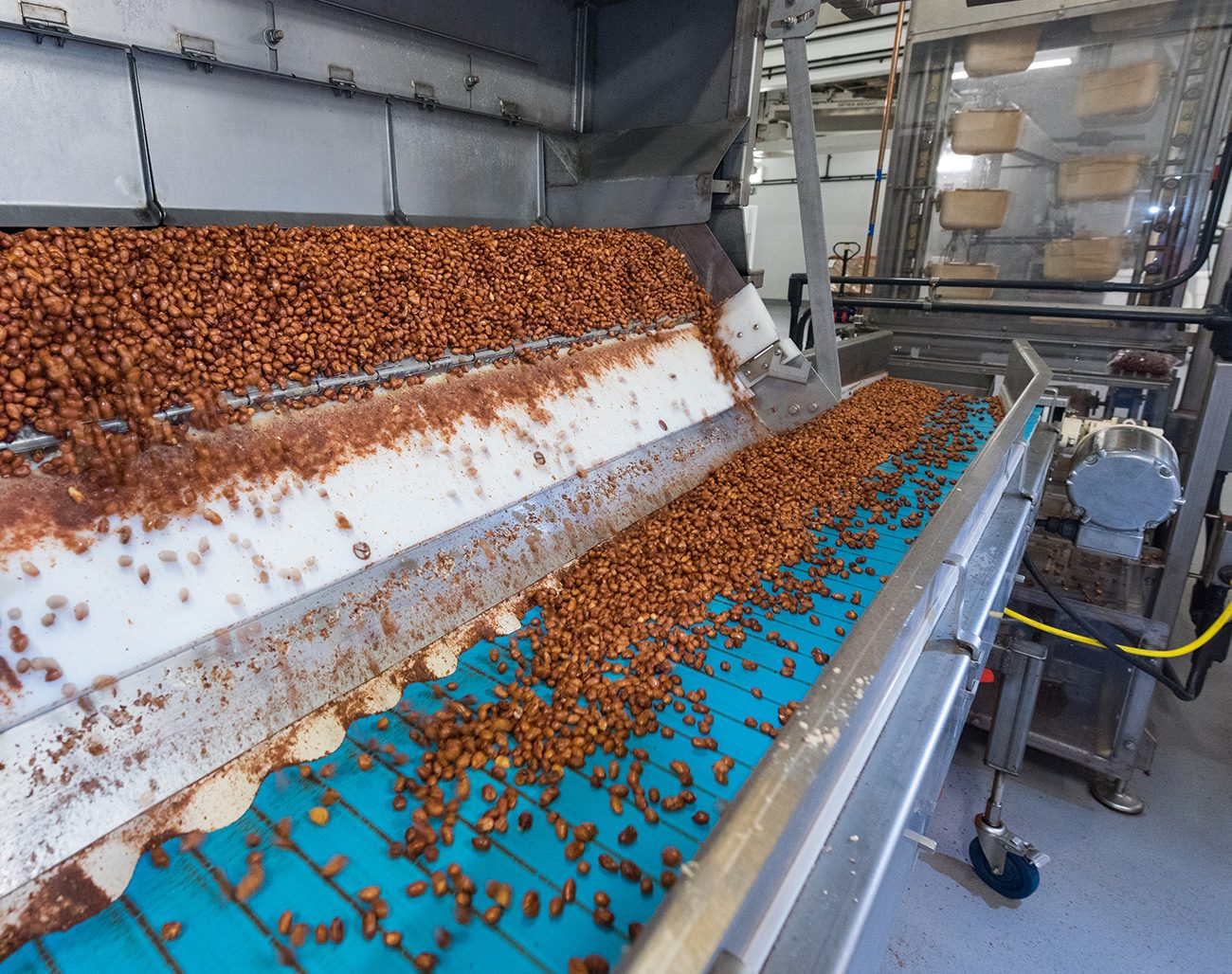
Roasted peanuts are on their way to candy and chocolate coating in this low-moisture plant. While the peanuts have become food-safe through the roasting process, conveyors can be kept sterile by exposing the underside of the belt to UV-C light. Photo courtesy of Imagemakers Inc.
Environmental air is another application for UV-C light. According to Diversey’s Tardioli, UV-C air disinfection systems are designed to work continuously and can be running during production and in the presence of operators without safety risks.
Use Multiple Technologies to Tackle Listeria
We should not look into one solution only to control, mitigate and potentially eradicate listeria from the food production floor. The use of chlorine dioxide, for example, can indeed be a good solution for biofilm removal in CIP applications (cleaning of closed circuits, pipes, tanks and vessels); however, this has limited uses in open plant cleaning (OPC) applications — cleaning of open surfaces, like open machines, conveyors, tables, floors, walls, etc. Chlorine dioxide, in fact, is a gas, unstable in aqueous solution and has some toxicity concerns, hence is best used in closed and confined circuits.
For OPC, the recommended elements might be the use of pressurized systems at medium pressure (max 40 bars), as these will provide a mechanical effect on the surfaces to remove a large part of the contamination; an adequate formulated detergent should then be applied — this should cope with the organic contamination and the inorganic compounds present in the water or in the contamination, the material and many other aspects. The cleaning step should be then followed by a terminal sanitization or disinfection with a biocide validated for the intended application. Since these operations are generally manual, it’s important to have a plan for validating the SSOP, verifying its execution and monitoring the parameters to make sure you adhere to the conditions that were validated in the first place.
Finally, a key aspect to food safety is equipment and site hygienic design, as these should have several specific construction characteristics that will allow their correct and complete cleaning and sanitation. This aspect was much more overlooked in the past, but through EHEDG and 3A, for example, there are many guidelines that help businesses comply with the latest and modern standards.
—Fabrizio Tardioli, associate director, Global Marketing Food and Beverage, Diversey, a Solenis Company
Ozone and Plasma Technologies
Ozone and plasma cleaning are promising chemical-free sanitation technologies that offer effective microbial reduction in various food processing applications, Khinouche says. Ozone is a powerful oxidizing agent that effectively destroys bacteria, viruses and biofilms.
Ozone is currently being utilized in large-scale food processing facilities in both gaseous and aqueous forms for surface and environmental sanitation, says Matt Lowe, president and CEO of Advanced Ozone Integration. Centrally installed aqueous ozone systems (systems that provide ozone dissolved in water) are designed to apply ozone to multiple applications, including in-process direct treatment of food products (raw and RTE), in addition to indirect application on food processing equipment. The same system then provides ozone during the cleaning/sanitation shift via spray gun hose stations for any open plant cleaning (OPC) activities.
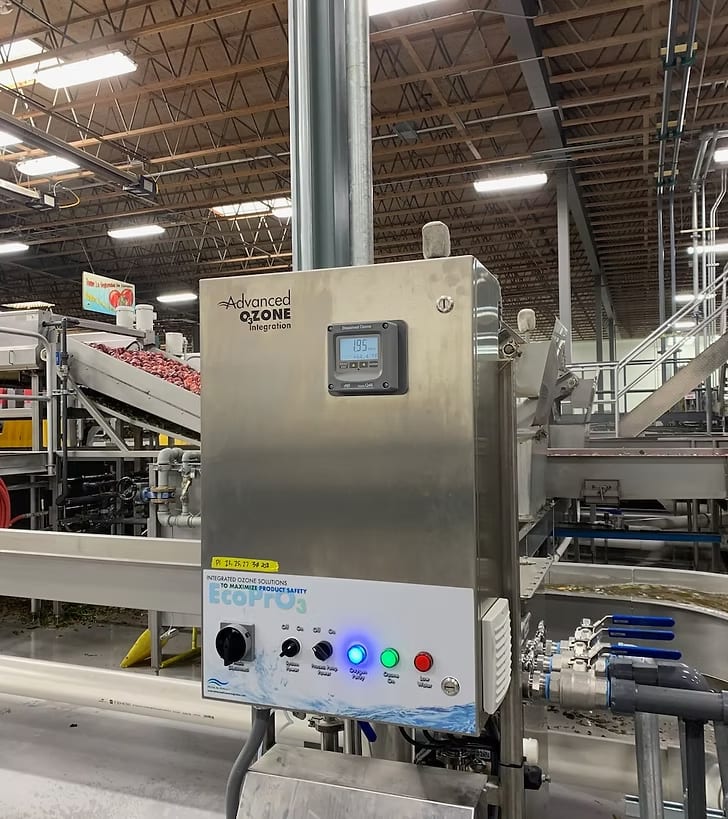
The Advanced Ozone Integration EcoPrO3 Aqueous Ozone Family is a state-of-the-art, non-thermal, aqueous ozone antimicrobial treatment system designed for surface sanitation of products and equipment. The system capacities range from 20 to 150 gallons per minute of aqueous ozone solution (ozone dissolved in water). All systems include remote monitoring, data logging and system notifications, and they are FDA, USDA, USDA Organic Program and EPA approved. Photos courtesy of Advanced Ozone Integration
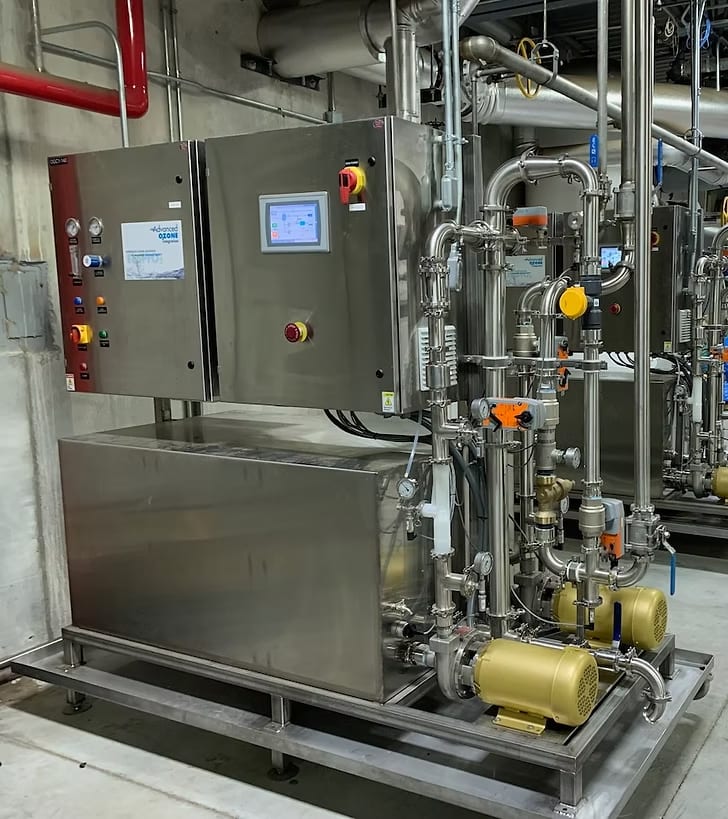
In addition, some facilities are starting to explore aqueous ozone use for CIP and COP as a replacement for traditional sanitizers in the final sanitizing step of the CIP or COP process. Many processors successfully utilize aqueous ozone to specifically target listeria harborage areas, like floor drains. Ozone gas is also being utilized for facility environmental treatment and has been proven to treat a variety of microorganisms — including the listeria species — in hard-to-reach areas, such as refrigeration units and their drip trays. From a green standpoint, ozone is a standout. It is an oxygen-based molecule that only requires air and electricity to generate on-site, leaving only oxygen behind as a byproduct, Lowe adds.
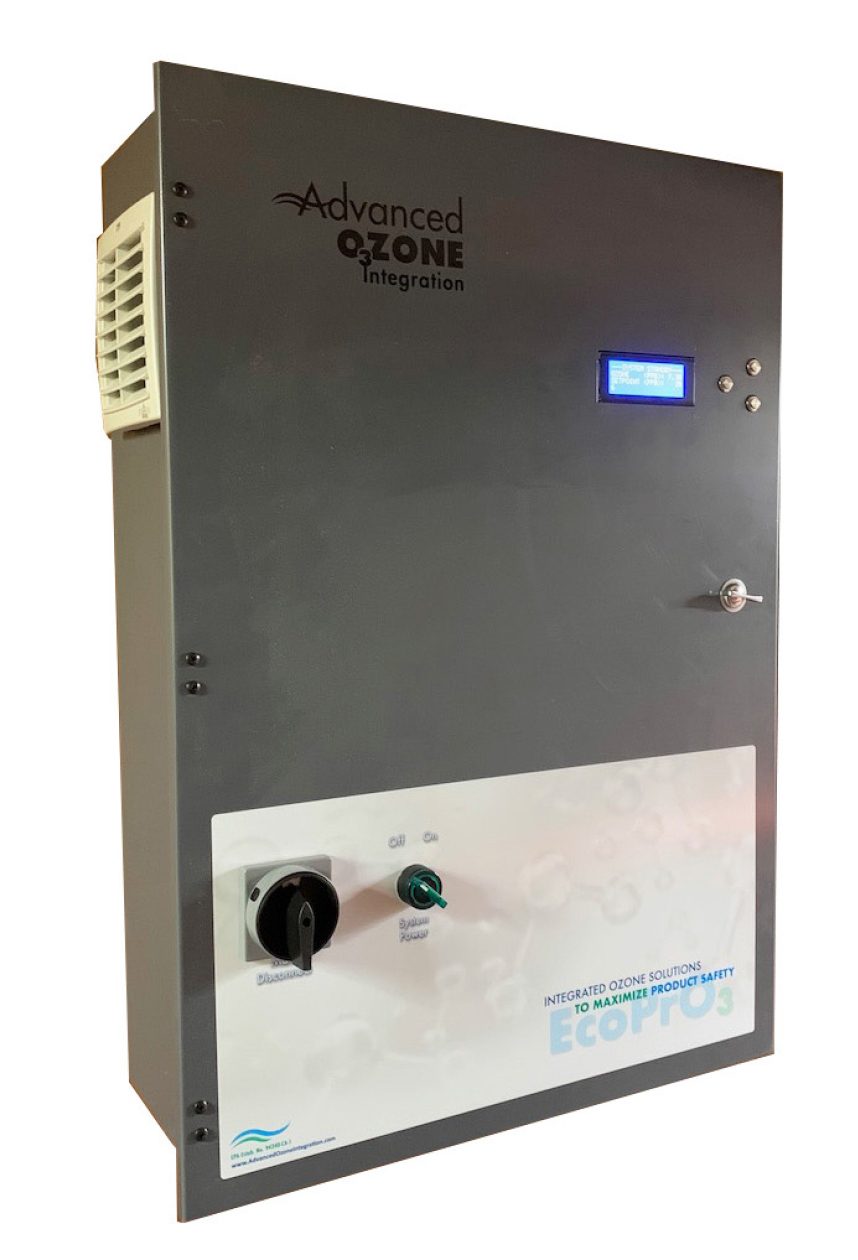
The Advanced Ozone Integration EcoPrO3 Gaseous Ozone Treatment Systems are designed for extremely accurate setpoint gaseous ozone treatment of products and surfaces for mold and bacteria control. The systems produce ozone gas at a rate of 10 (right) to 150 grams/hour (left), have an integrated UV absorption technology ozone concentration monitor with a sample pump for setpoint control of ozone concentration in the space being treated, and are FDA, USDA and USDA Organic Program and EPA approved. Photos courtesy of Advanced Ozone Integration
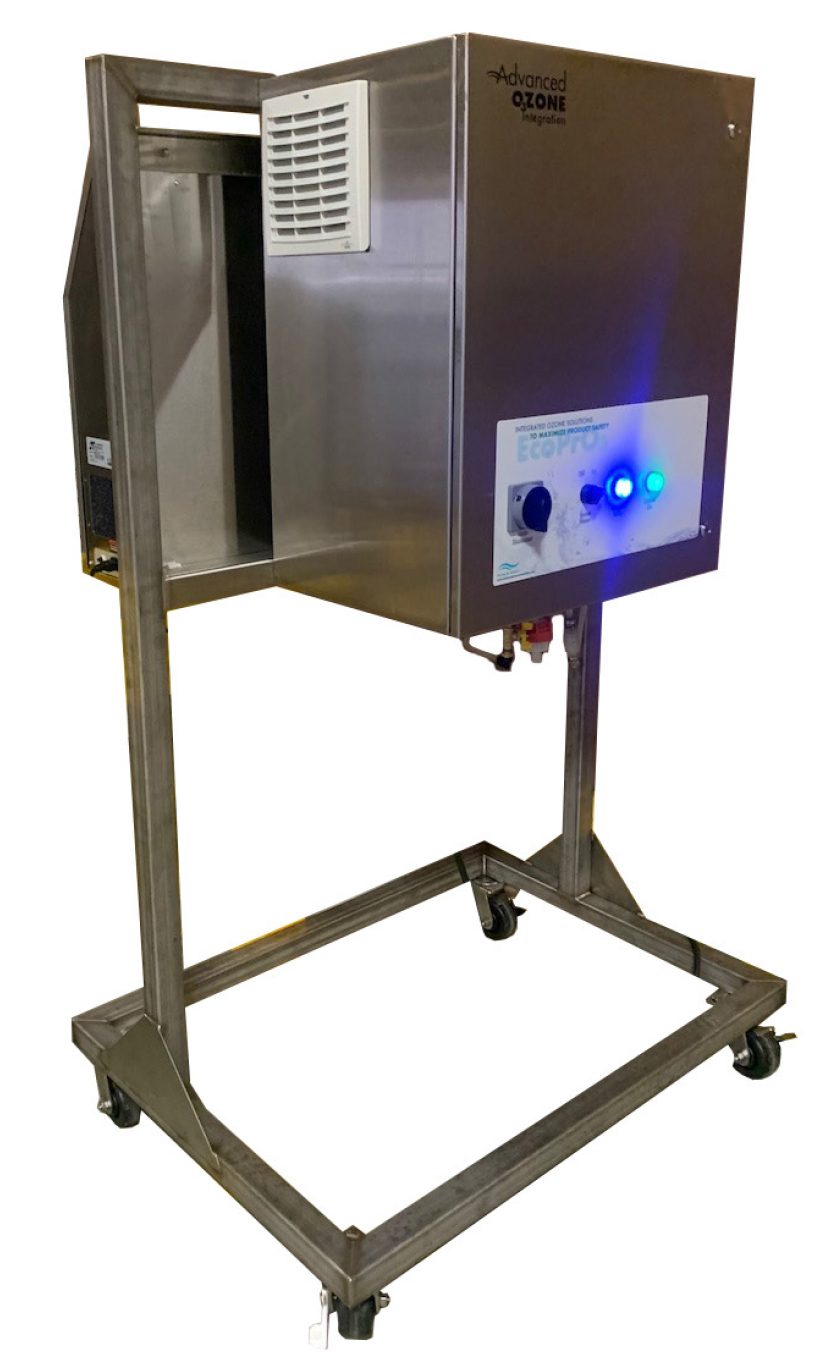
“We have seen ozone tested for CIP applications but not penetrate the market versus existing CIP chemistries,” says Diversey’s Tardioli. However, plasma as atmospheric pressure plasma torches can be used in cleaning, as well as sanitation of open, hard surfaces. Plasma systems may work well with robotic arms and automated systems but require a high capital investment and are typically limited to thin soil layers only. Because of that, they might work well in sanitizing an already clean and dry surface; however, they will not cut through a millimeter of soil layer. Also, air extraction might be required for operators nearby.
Plasma-based sanitation generates reactive oxygen and nitrogen species that can effectively inactivate pathogens on surfaces and in the air, says Novolyze’s Khinouche. “This technology is especially useful in environments where traditional wet sanitation is impractical, such as dry processing facilities for low-moisture foods (e.g., bakeries, snack manufacturing and powdered ingredient production). Plasma cleaning can also be applied for packaging sterilization, ensuring extended shelf life without the need for chemical preservatives.”
Choose the Right Technologies for Your Application to Control Listeria
Listeria monocytogenes (with two new outbreaks in March and unknown sources) can be pesky to control, as we’ve already discussed. System integrators and chemical suppliers stand ready to help with the technology solutions you need — no matter the bacterium.
Resources:
“Listeria monocytogenes – How This Pathogen Survives in Food-Production Environments?“ Jacek Osek, Beata Lachtara and Kinga Wieczorek; Frontiers in Microbiology, 26 April 2022, NIH
“Introduction to the Microbiology of Food,” Texas A&M AgriLife Extension, College Station, Texas; accessed 25 March 2025.
“The Importance of Post-Construction Disinfection in Food Processing; Chlorine Dioxide Fumigation” Jay Parks, PureLine, accessed 27 March 2025