NovemBER 2022
From Berry Farming to the Deep Freeze
Fabulous Food Plants
by Derrick Teal, Editor-in-chief
Hiroki Koga, CEO and co-founder of Oishii, inside the company's latest vertical farm, reportedly the largest vertical farm for strawberries in the world. Photo courtesy of Oishii
For our coverage of Fabulous Food Plants this year, we decided to do something a little bit different in honor of “plants,” aka flora. When we think of food plants, we almost immediately think of processing facilities, but there’s so much more to food production than the processing plant. So, seeing how plant-based foods are altering the ways consumers think about protein, we decided to alter the way we think about food plants. The facilities we included this year are decidedly not processing facilities or plants in the traditional sense—but they’re definitely fabulous.
Oishii
Vertical farming has the potential to be one of the biggest innovations in farming. To that end, Oishii created its largest and most technologically advanced vertical farm yet to meet the growing demand for the company’s Omakase Berries.
Located in Jersey City, N.J., the new farm spans more than 74,000 sq. ft.—the largest vertical strawberry farm in the world, according to Oishii—to exclusively grow the company’s strawberries. The company repurposed a former Anheuser-Busch factory, transforming it into the company’s flagship farm of the future and new headquarters.
Oishii’s vertical strawberry farm is opening doors for a different variety of vertically farmed produce, and Americold’s facility in Dunkirk, N.Y., was built with LEED certified energy efficiency in mind.
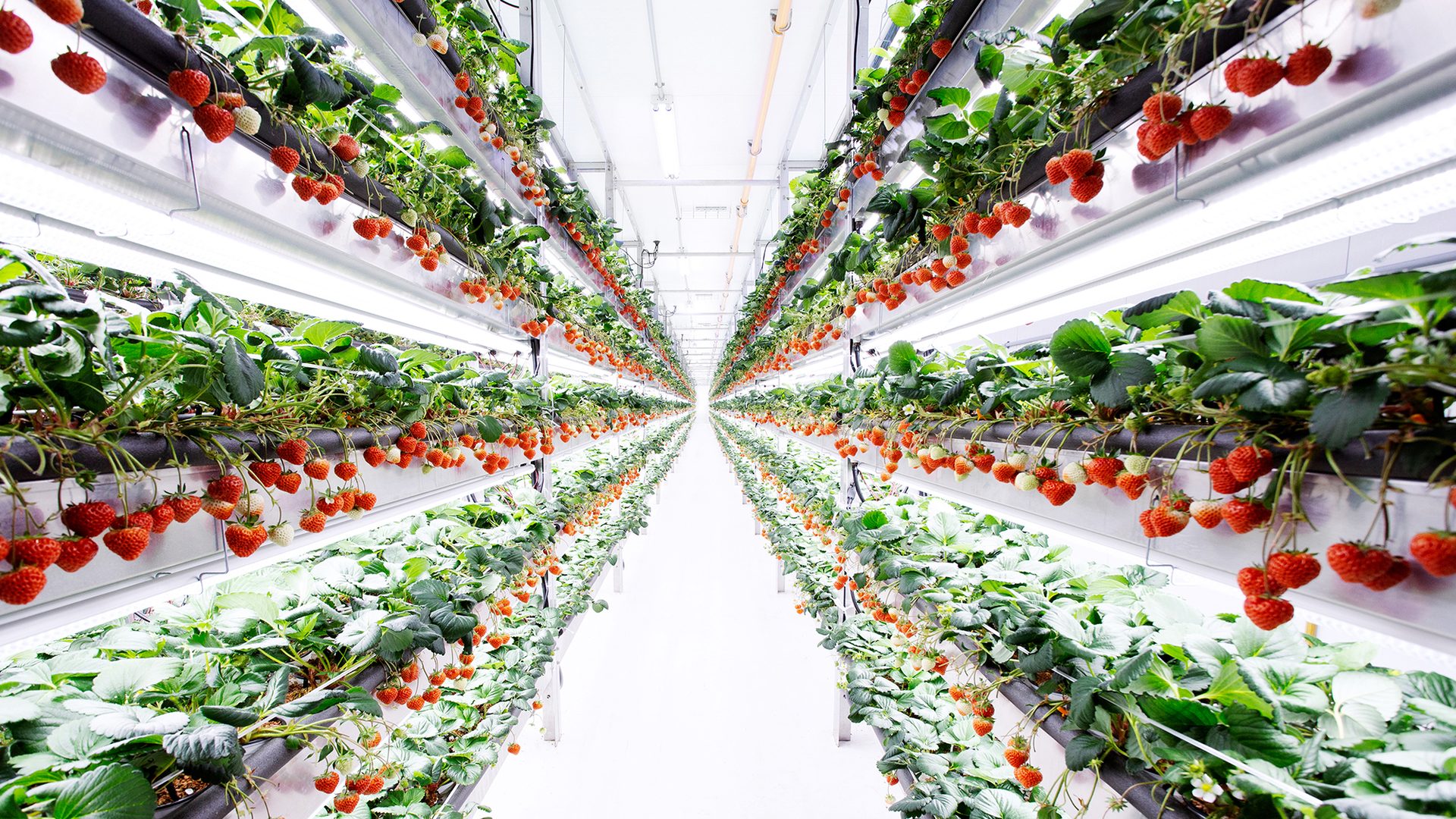
The self-contained nature of vertical farms creates optimal growing conditions for the product, while also allowing for greater water and energy efficiency. Photo courtesy of Oishii
Oishii introduced the Omakase Berry in 2018, noted for its sweetness, aroma and creamy texture. The Japanese cultivar is grown in Oishii’s three indoor vertical farms, which are designed to harmoniously marry nature, technology and farming techniques perfected for decades in the foothills of Japan. The company says it has recreated the elements—rain, air, heat, light and nourishment—to grow the perfect fruit every time, all year round. The company says it perfected the fruit through its first-of-its-kind pollination method, conducted naturally with bees. The hyper-locally grown produce is farmed without pesticides. Harvests rely on advanced robotics and automation, while using 60% less energy and 40% less water than the company’s first-generation technology. Oishii says that use of these innovations in conjunction with its farming methods allows the company to pass on significant value to its customers.
“At Oishii, we are committed to revolutionize the future of food by offering the best-tasting produce, grown in a way we believe is better for people and better for the planet,” says Hiroki Koga, CEO and co-founder of Oishii. “We’ve worked hard to pioneer advanced technology that unlocks a substantially more efficient way to grow our unrivaled strawberries. Our largest farm yet pairs the next frontier of indoor farming innovation with the care and precision of centuries-old Japanese farming techniques.”
The company says it is currently in development on new strawberry varietals, as well as other types of flowering produce and vine fruits, such as tomatoes, melons and peppers.
Americold
In June of this year, Americold announced the grand opening of its newest facility in Dunkirk, N.Y. This 181,000 sq.-ft. cold storage and operational space features 25,000 pallet positions to support cold storage needs in the western New York region.
“This is our first facility in western New York, and we’re excited to expand in this area at the request of our customers,” says George Chappelle, CEO, Americold. “Our goal is to provide the best-in-class service to all of our customers and this facility will help us to do that in New York.”
Located on Williams Street, near Arrowhead Drive in Dunkirk, it is the most recent addition to the company’s portfolio of 250 locations around the globe, employing more than 60 full- and part-time associates.
But what sets this facility apart is its LEED certification. This is Americold’s second LEED certified new construction project, having received LEED Silver certification for a 311,000-sq.-ft. freezer project in Savannah, Ga. That project utilized a similar design and construction process and environmentally friendly systems.
Operationally, this facility is designed to store frozen products at -20°F. “We’ve installed specialized equipment designed to operate in this extreme temperature within the warehouse to support efficient picking operations (selecting product from pallets to be delivered to stores grocery stores, restaurants, etc.),” says Doug Karmel, vice president global construction for Americold.
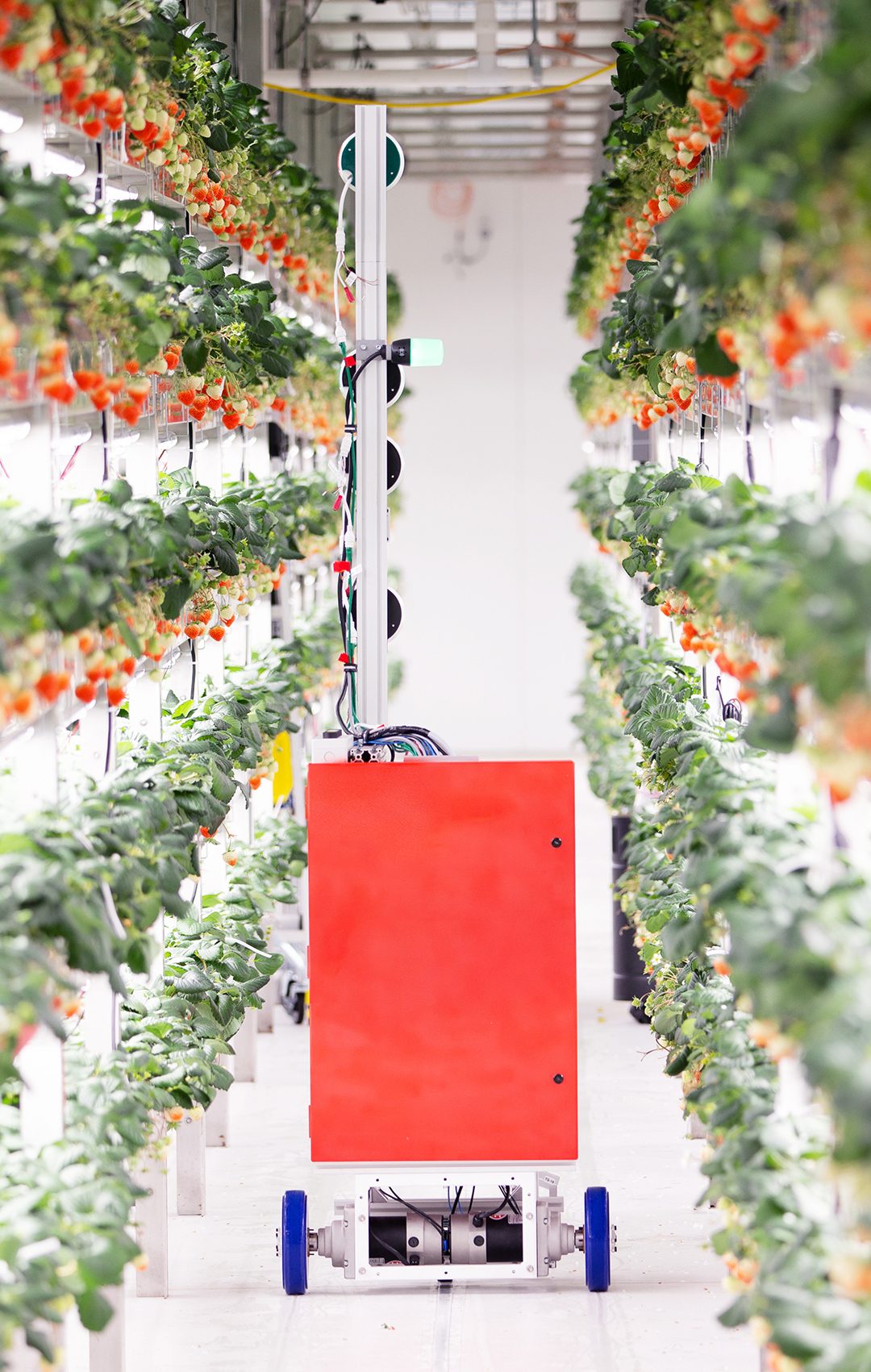
Oishii's vertical farming operations employ robotics and automation to enable fewer staff to do more, and do it more accurately. Photo courtesy of Oishii
Housing such intense conditions could’ve been a nightmare for the company’s energy usage, so achieving LEED certification, which takes into account energy consumption, is quite the feat. As mentioned earlier, the Dunkirk facility was patterned off of Americold’s Savannah facility. Since achieving LEED certification was in the cards from the outset, the project team needed to focus on ensuring the facility’s energy efficiency.
“Although freezer facilities tend to be high energy users, they are designed with a highly insulated thermal envelope and are vapor sealed,” says Karmel. “This building was designed to utilize ALTA Refrigeration ‘Expert’ Units for the refrigeration of the warehouse. These units are designed with variable speed drives to deliver only the amount of energy needed to keep the space at temperature. Additionally, the packaged rooftop Freon ‘Expert’ units have proved to be much more energy efficient than the prototypical Ammonia-based engine room systems. These units are air-cooled, which eliminates the use of water required to cool the ammonia systems. The utilization of the ALTA systems provided 12 out of 18 possible points in the Optimize Energy Performance category in the LEED design category.”
"The utilization of the ALTA systems provided 12 out of 18 possible points in the Optimize Energy Performance category in the LEED design category." — Doug Karmel, Americold
Those energy-efficient freezers are believed to be the future of the industry by Americold and its building partner UISC, LLC, the design/builder for the Dunkirk facility. Americold has set environmental goals, which are outlined in its ESG Report, and one of those goals is to achieve LEED, BREAM or country-specific equivalent certification for all new construction projects. DBHMS consulted on the LEED certification.
With the energy efficiency taken care of, the material shortage striking all construction projects the past few years that presented the biggest challenge.
“The greatest challenge faced was finding materials and equipment that could fit our project schedule and our sustainability goals,” says Karmel. “Construction began in June of 2021 and needed to be finished in May of 2022. This is the period that COVID had it greatest impact to the global supply chain and construction labor availability. This aggressive timeline limited what we were able to use for building materials.” FE
NOVEMBER 2022