Maintenance Strategies - Part 1
Even with the best strategy and sensors in place, the final result comes down to humans making the right decision.
Have a Strategy in Place…Or Put Out Fires, Maybe Literally
Maintenance:
Maintenance strategies are often categorized as reactive (wait until it breaks), preventive maintenance (PM), reliability centered maintenance (RCM), risk-based PM, condition-based monitoring—otherwise known as predictive maintenance (PdM)—and prescriptive maintenance, which uses analytics—such as AI—to indicate equipment is headed for trouble, and can prescribe and prioritize mitigation and/or repair).
You may think you have a well-defined maintenance strategy in place, which for example, uses sensors to track bearing temperatures on a critical 200 hp motor and has operators informed on what to do when bearing temperatures rise. But a bad decision in taking action can do more than shut down a line; it could be disastrous. A good example is last winter’s Norfolk Southern freight train derailment with a hazardous chemicals spill and resulting fire in East Palestine Ohio. And you can’t say they didn’t have data.
Even with track temperature sensors in place and spaced 11 miles apart, Norfolk Southern failed to slow down and stop the train before the 23rd car of the 149-car train experienced a sharp rise in wheel bearing temperature to more than 250°F above the ambient outdoor temperature of 10°F. According to an NPR report, the initial findings of the NTSB showed that the first track sensor to indicate a temperature rise recorded a temperature 38°F above the ambient; a second sensor farther east, 103°F; and a third sensor, 253°F. 1
Train company guidelines suggest a take-action point when wheel bearings reach 170°F above ambient. Once a temperature of 200°F is reached, operators are required to stop the train immediately and remove the car. Unfortunately, by the time remote dispatchers issued an E-stop to the train’s engineer, the bearings on that car had begun to seize, creating an uneven stop and derailment—and resulting fire. One has to ask, though armed with the rising temperature sensor data, why didn’t the railroad see a trend developing that could have resulted in an early warning to slow and stop the train gently before bearings seized on the 23rd car?
Modern CMMS software, like eMaint, can integrate with condition monitoring sensors and tools, triggering word orders based on asset health data. Image courtesy of Fluke Reliability
by Wayne Labs, Senior Contributing Technical Editor
Factors That Can Hinder Good Maintenance Strategies
As with the railroad, food and beverage processors may have the beginnings of a good maintenance strategy in place, but several issues can complicate the administration of it. For example, here’s a quick dozen:
• Poor equipment reliability and downtime reduction
• Aging infrastructure
• Talent shortage and skills gap
• Technology adoption is slow
• Robust data management and analytics is needed
• Budget constraints inhibit good maintenance strategies
• Regulatory compliance and machine safety/food safety
• Sustainability and energy efficiency
• Supplier relationships and spare parts management
• Communication and collaboration
• Poor change management and control
• Lack of remote monitoring capabilities
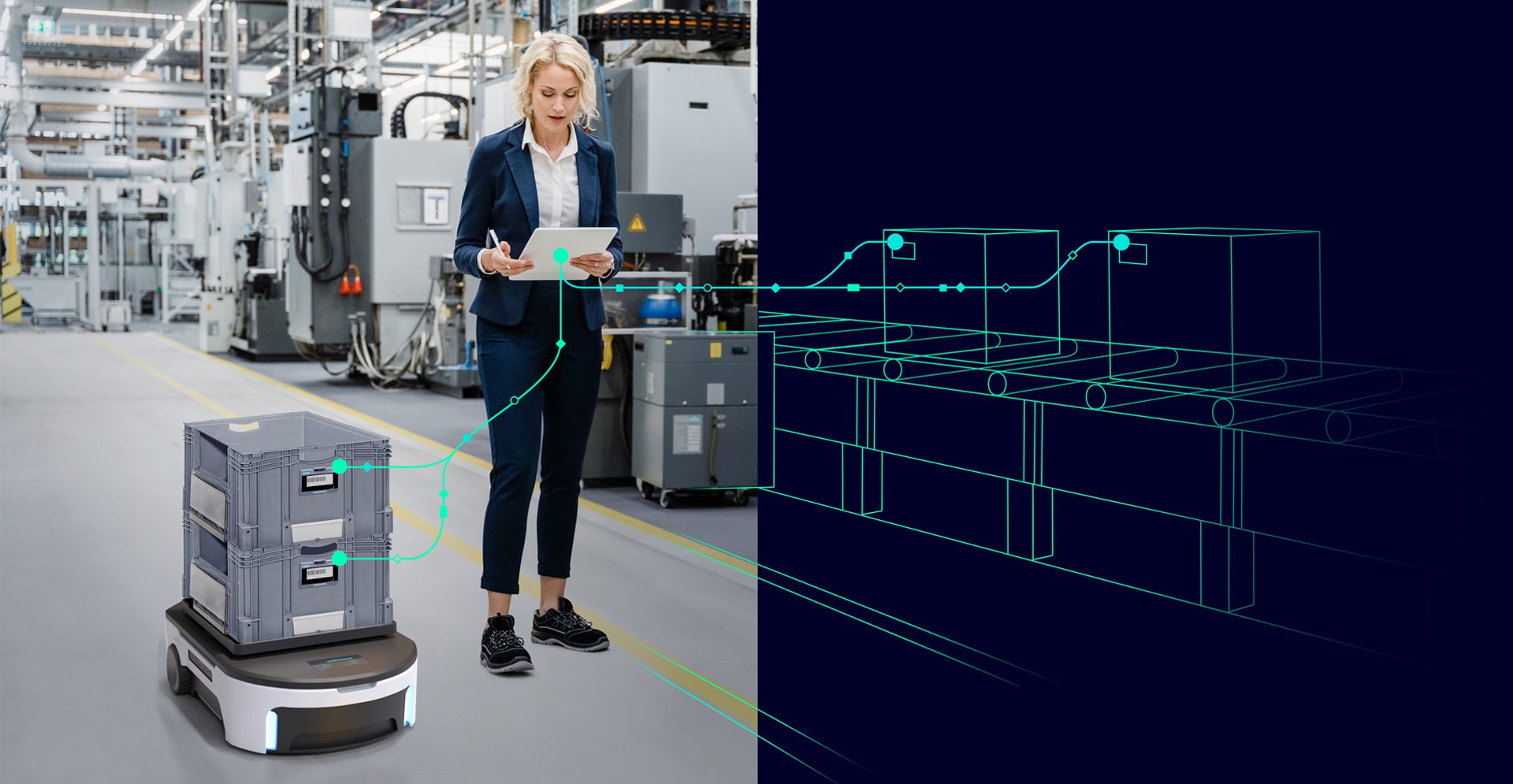
Sound maintenance strategies are dependent on accurate data from multiple sensors integrated in a cohesive software environment so technicians know where to most efficiently focus their efforts. Image courtesy of Siemens
Strategizing Maintenance around Major Issues
What do maintenance providers, engineering houses and sensor manufacturers see as the main stumbling blocks/needs in the above list? Corey Cronin, director of business development, food & beverage | packaging at Emerson’s Discrete Automation Group, lists three. Equipment reliability and downtime reduction, asset utilization, and OEE are critical KPIs driving maintenance managers’ efforts to get as much out of their equipment as possible, making sure it is as reliable and efficient. “Sustainability and energy efficiency are an equally important driver and concern. Many of our customers are particularly focused on reducing plant air consumption, which in some facilities can be up to 30% of the total energy used in the facility. They are investing in point-level power monitoring and air monitoring systems that provide real-time data to drive preventive maintenance practices and efforts to eliminate pneumatic leaks in as many areas as possible.”
Cronin also notes that talent shortage and loss of skilled operators are food processors’ number-three concern, and there has been increased interest in improved SCADA platforms and machine data reporting tools so processors have the information to respond to downtime activities and can better prepare for and plan maintenance strategies.
“The most pressing maintenance issues I see food and beverage clients face are equipment reliability and downtime reduction, aging infrastructure, and talent shortage and skills gap,” says David Ziskind, Stantec market lead, food & beverage. “Ready, willing and able labor talent is important (skilled and available). Infrastructure may be aging or on a long capital replacement cycle. On the positive side, I see more clients dig deep from the sustainability and energy efficiency angle when replacing equipment, although I don’t often see equipment replaced prematurely to capture this, unless it offers a very compelling ROI.”
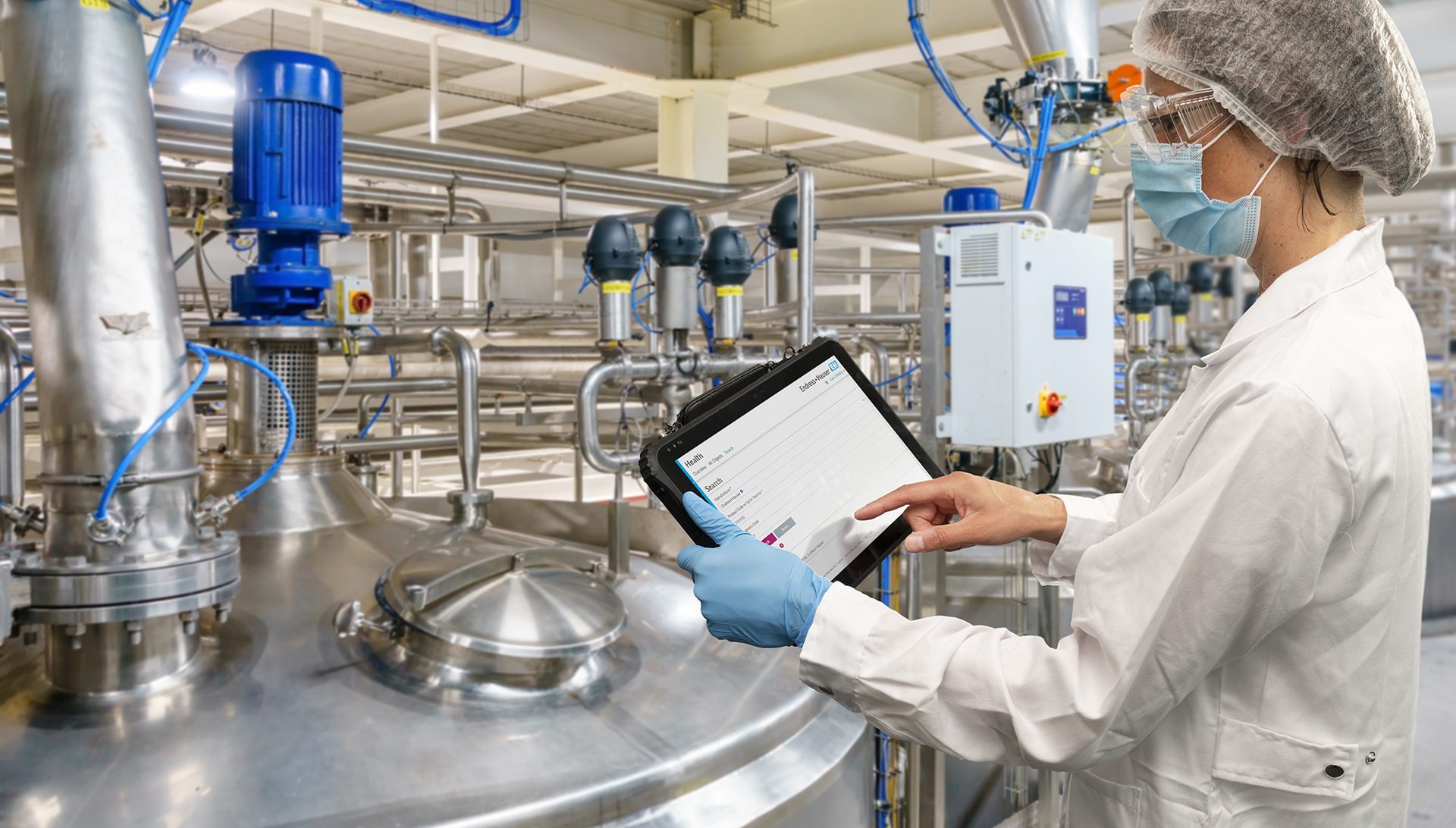
A maintenance technician uses Endress+Hauser Netilion Health instrument maintenance software on a Field Xpert wireless mobile tablet in a food and beverage plant. Image courtesy of Endress+Hauser
Though not directly stated on the list, calibration and documentation activities are major concerns for processors, says Jason Pennington, Endress+Hauser USA director of digital solutions. “More frequently, however, these discussions are trending toward installed base analysis, standardization and digitalization strategy co-development. We are in a time void of a straightforward approach. However, there are core themes such as empowering technicians and working toward a more predictive future [plus] overall continuous improvement through data analytics—all of which are leading initiatives and projects.”
Modern technology adoption is a key issue that goes hand-in-hand with talent shortage and the skills gap, says Gregory Perry CMRP, CRL, eCMP, Fluke Reliability senior capacity assurance consultant. As technology becomes more human centric, it is inevitable that it marries with the asset centric realms. Not to be seen as a replacement for talent shortage, artificial intelligence, machine learning and edge computing are steadfast to augment the skills gap. Merging the best of technology with the best of human capital is a win-win, Perry adds.
Erin Sidwell, Fluke Reliability key account manager, food and beverage/process manufacturing, chose equipment reliability and downtime reduction, talent shortage and skills gap, and data management as three top concerns. “Food and beverage companies look for solutions that simplify food safety and regulatory compliance [and] keep production lines moving. Digitization of work orders, standardization across the organization and automation push to end unplanned downtime and sustainably meet customer demand.”
Replacement parts in equipment and pumps that come in contact with food must meet FDA’s CFR 21 Part 77 regulations. Pump and pump parts suppliers, like Anderson Dahlen (A Gray Company), work with food companies to ensure that the correct parts are ordered and shipped, according to Kris Rarden, business development manager.
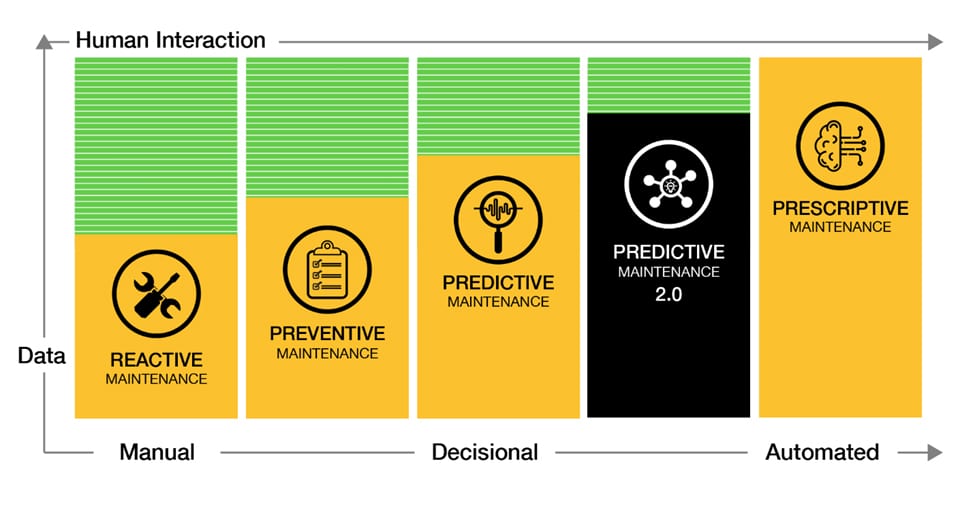
Maintenance strategies require less human interaction as automation increases. For example, reactive maintenance requires the highest level of human involvement, but fully data-driven monitoring (prescriptive maintenance) requires no human interaction to make a diagnosis. Image courtesy of Fluke Reliability
Two items on the list create tricky problems for processors, according to Jeremy Reed, manager, instrumentation, Gray Solutions, A Gray Company. Aging infrastructure and equipment and reliability/downtime reduction are two areas that often present related issues—as new technology emerges, some of the older software and hardware can become scarce, expensive, or even obsolete. The processor can’t pivot overnight so a lot of these older components are required to keep running. This means more wear and tear along with less downtime for preventative maintenance. Paying special attention to maintenance metrics such as MTTF (mean time to failure) in these situations can help end users understand the limits of their systems and better determine schedules for maintenance. Over-running or under-maintaining can turn into an exercise in diminishing returns—especially when the parts in question are part of an aging infrastructure.
But aging infrastructure isn’t just equipment like large motors or HVAC systems. “Interestingly, it’s the aging infrastructure of our customers’ buildings that often creates the greatest challenge,” says Brad Moore, principal of reliability at Pinnacle Reliability. “For example, one of our customers experienced a leak in the roof of one of their buildings, forcing the facility to stop production.” End of Part 1