mobile devices - Part 2
Mobile devices give operators freedom to move about, but user interface design needs careful thought before implementation.
on the Plant Floor to Maximize Operator Efficiency
Deploy Mobile Devices
Optimizing Mobile Devices and Alarms
The first step in optimizing the UI for effective alarm monitoring is to conduct “Alarm Rationalization” on the system, distinguishing alarms from alerts, says CRB’s Vortherms. Alarms necessitate operator intervention, while alerts provide information or are part of the standard process.
When designing UIs it is important to understand the priority of the data to identify the most critical parameters that operators must monitor and to have a hierarchy of needed alarms, says Ponzellini. “Emerson’s Movicon.NExT provides a solution for configuring and sending alarm and event notifications to designated recipients, including on-call personnel, called Alarm Dispatcher. Using this solution, you can specify which events and alarms trigger notifications and choose the recipients. This is accomplished through various communication plugins, such as SMS, Email, VoIP, Telegram.”
Emerson’s Movicon.NExT software platform provides personalized visualization solutions via WebHMI, web clients, and augmented reality, supporting a wide range of user needs throughout all industries and applications. Image courtesy of Emerson
by Wayne Labs, Senior Contributing Technical Editor
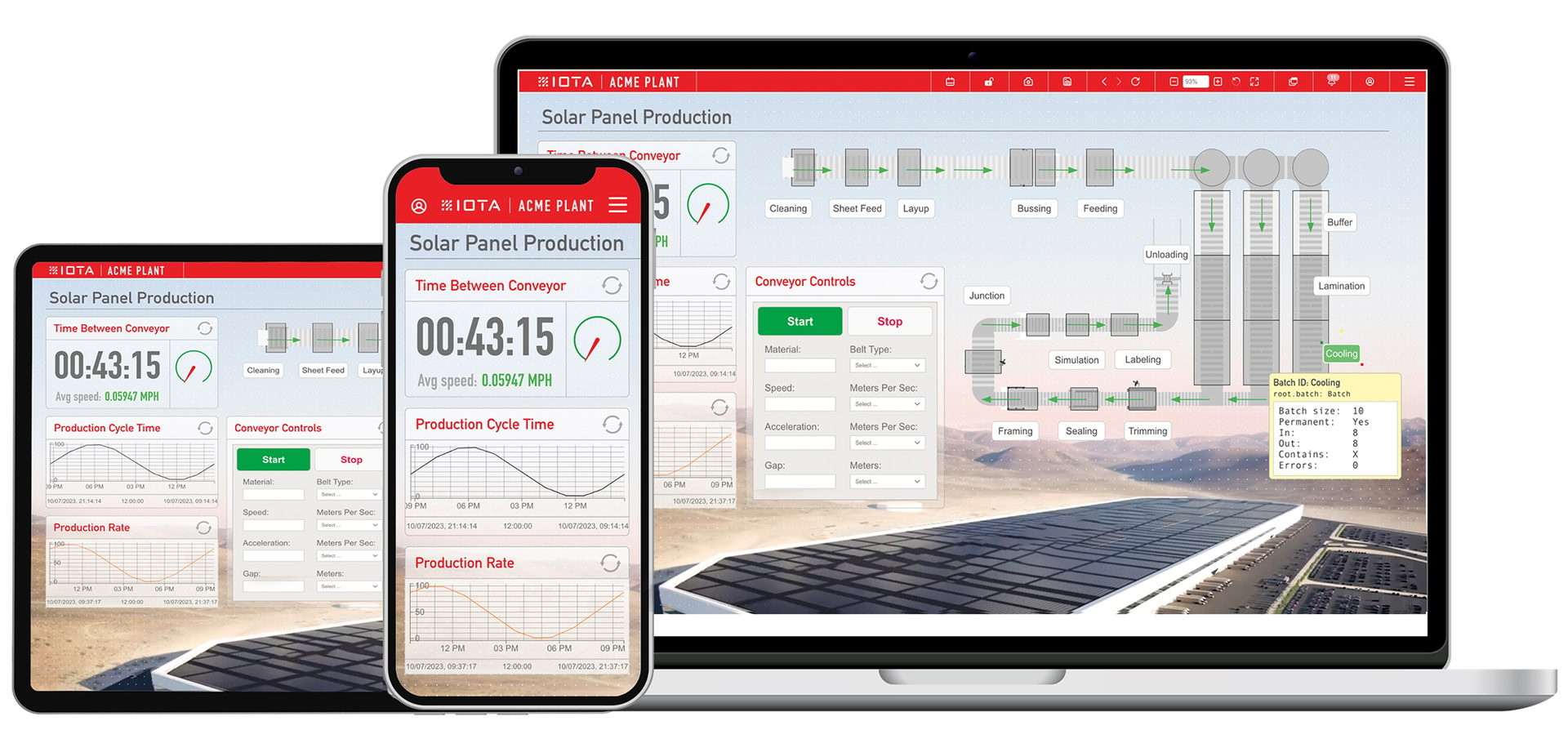
IOTA Software developed Vue as a dynamic process visualization and analytics platform, able to seamlessly integrate data from all aspects of a business and empower users with intuitive self-service graphics and dashboarding viewable on any target device. Image courtesy of IOTA Software
How do you physically get the operator’s attention when an alarm condition comes up in a noisy environment? If operators are equipped with mobile devices and the plant floor noise levels are high, one option is to use Bluetooth-enabled, noise-canceling headphones, says Vortherms. These headphones protect the operator’s hearing while enabling message transmission or alarm notification. Integrating human-generated messages would require additional integration with the system. Another commonly used option in noisy environments is the use of lights to signal alarm conditions to operators. If operators have mobile devices with tactile notifications (vibrate), these can also be used to notify them of a text message or email from the control system.
“We typically do not recommend headphones for use on the plant floor for communication or notification of alarms or status,” says Gray’s Weekley. The use of earbuds and many other headphone-type devices would not fit many manufacturers’ material safety policies. In addition, headphones typically provide a safety concern due to the distraction they would provide to the ability to communicate effectively in key situations.
“In the plant environment, we typically propose and implement alarm notification via HMI screens with a combination of ISA 101 style alarm depiction and ISA 18.2 guided alarm management to provide operations with key alarm information in a prioritized manner,” says Weekley. “For key alarm scenarios that require more immediate attention, we often will implement light stacks to give visual indication to the existence of a problem. On the plant floor, audible alarm horns may also be installed, but we typically reserve the implementation of these devices as a last resort.”
Another option is the use of large, overhead easy-to-read displays/monitors, which allow operators to quickly identify alarms and their source, says Slowik. “I imagine quite a few manufacturers still use visual alerts (attention-grabbing colors and flashing) because they are more reliable in noisy environments and can be integrated into the machinery itself.”
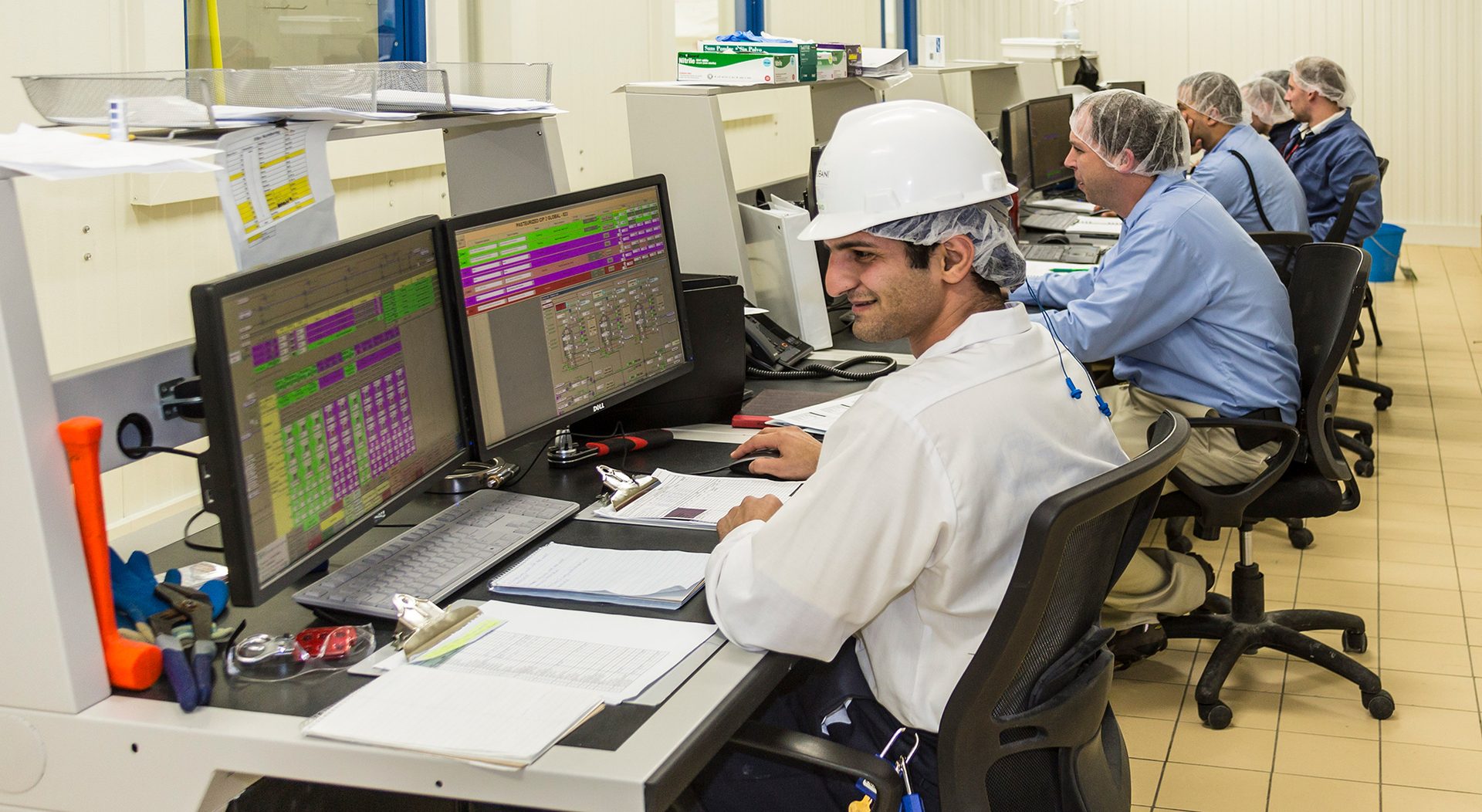
In a control room at a large food processing facility, operators supervise the entire system from mixing, blending, processing, packaging, etc. On a mobile device, only the most relevant data will be shown to the user, and that data will usually be applied to that person’s specific job role. Image courtesy of Bill Nichols
Looking Forward
Operations and maintenance assistance represent valuable applications for AR/VR technology when combined with mobile devices, says Vortherms. These technologies can be employed to enrich the information available to technicians or to facilitate remote subject matter experts (SMEs) in assisting from a remote operations center.
Suppliers like Emerson are already integrating AR solutions for its HMI/SCADA systems, for example its Movicon.NExT platform. With wearable AR devices like Android smart glasses and Windows 10-based HoloLens, operators can easily manage processes and access real-time data. AR systems usually complement traditional workstations rather than replacing them, says Ponzellini. For maintenance, AR systems let users view onscreen guides, like manuals and troubleshooting videos, and communicate with the operations center wirelessly. This helps prevent mistakes during procedures by giving users instant access to the right info.
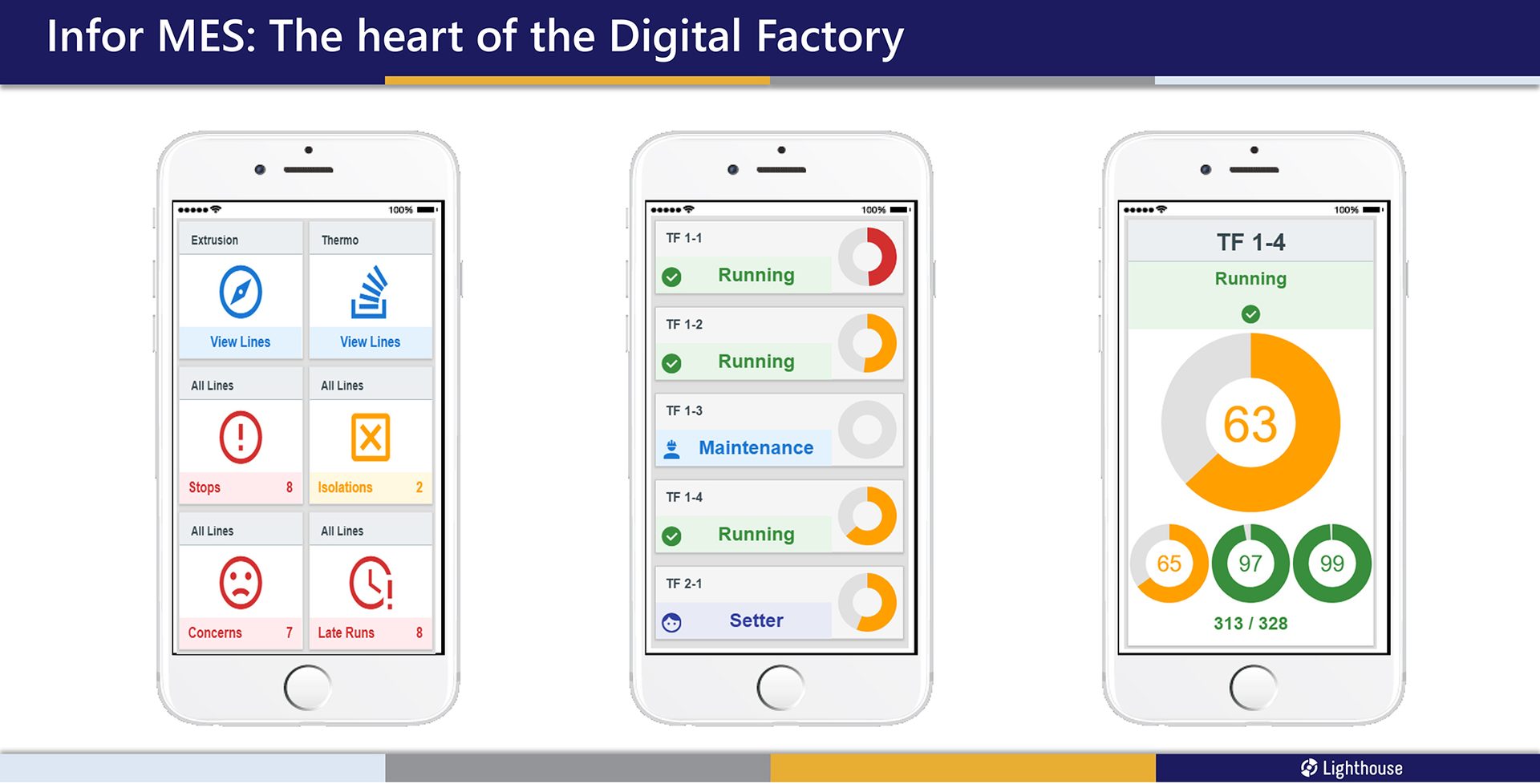
Smartphone screens are great at providing key data on the digital factory. Infor MES provides several views of machine status and KPIs while also showing line stops, concerns and line status. Images courtesy of INFOR
According to ICONICS’ Doto, the combination of AR and mobile devices will help operators/technicians to ensure product consistency by overlaying quality control checklists and guidelines onto products moving along production lines and guarantee quick and accurate completion of maintenance tasks through access to step-by-step instructions, diagrams and even remote assistance from experts.
With VR and mobile devices, operators and technicians will be able to create simulations to practice maintenance and repair procedures on virtual equipment. They can also create immersive simulations to practice operating new and unfamiliar machinery or deal with emergencies in controlled environments, says Doto.
Finally, in conjunction with mobile devices on the plant floor, the use of AI will give operators and technicians additional insight to process optimization, energy efficiency, predictive maintenance, and quality control, just to name a few, says Doto. For one, AI can analyze production data to identify areas to improve efficiency and send recommendations for process adjustments to operators/technicians. Additionally, AI can analyze sensor data to predict when maintenance is required. Operators/technicians can be alerted prior to issues, so they can take appropriate measures. AI is also being used for quality control to inspect products and predict which manufacturing aspect needs adjustment/attention. Overall, mobile-friendly technology allows operators/technicians in the food industry to have more flexibility when interacting with their systems. And with advanced software users can customize a set of features that best suits their needs. FE