OctoBER 2022
Plant Operations
Wayne Labs, senior technical editor
A concept by a 20th century architect points toward today’s digital transformation—bringing all systems in a plant together as a single integrated tool.
Today’s Connected plant: A Unified Machine for Making Food
Nestlé Nescafé deployed Schneider Electric’s EcoStruxure Asset Advisor to ensure always-on operational resiliency and efficiency at Nestlé’s soluble coffee facility in Toluca, Mexico. The system’s Asset Advisor makes all power systems visible and able to be remotely managed around the clock. The system allowed engineers to react and avoid three unplanned stoppages that would have costed up to $52,000 per hour. Photo courtesy Business Wire

In 1927 Le Corbusier, a Bauhaus period French architect, authored a landmark book entitled in English, "Towards an Architecture." In it he asserted that a house is a “machine for living in.” While that may sound not very human, his intent was to show that a house is a tool that we use to live and function—just as a chair is a tool to allow us to sit, or a drill to make holes. With all the smart systems in today’s modern house controlled by your PC, tablet or smartphone, Corbusier’s concept, I think, has been realized way beyond his dreams. Today, we control our connected house to do our bidding!
Like Corbusier’s concept of a house as a tool, today’s modern food plant is—or can be—a well-connected, digitally transformed machine that pulls together process, building, energy, manufacturing and enterprise control systems into a single integrated, well-oiled tool for making food or beverages. Processors are realizing that to be competitive, they need all the information they can get about their inputs (ingredients, energy, utilities, etc.), process, product quality, food safety and output(s). Extending digital transformation to accommodate all these systems and integrate their data into actionable information is what turns the whole plant into a single, competitive tool.
While many food plants have yet to begin this digital journey, today’s technology makes it easier to connect and unify these systems than in the recent past. And processors who are building new plants see the necessity for connecting as many systems as possible to be well informed of the status of their facility, process and product.
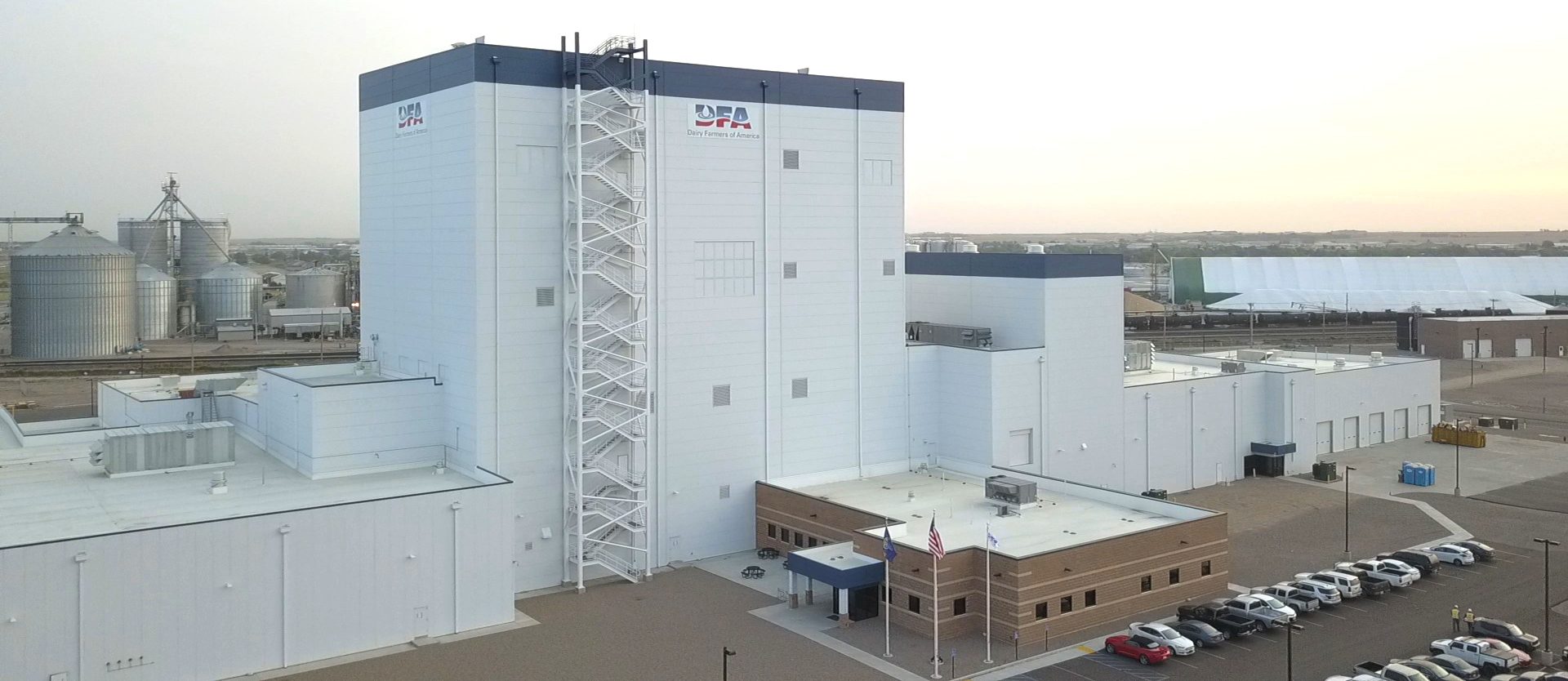
Dryer operations are where HVAC and process controls merge into a single system to save energy and be more efficient. Awarded FE Sustainable Plant of the Year in November 2018, Dairy Farmers of America’s Garden City, Kan., facility’s HVAC provides MERV-13 filtered clean air for wet processing, evaporator and tower spaces. Photo courtesy DFA
Start Planning With Broad Expertise
New network technologies with standardized communications make integrated systems easier to configure, build and connect to other systems such as building and HVAC systems. Automation vendors now provide AI and digital twin technologies plus digital analytics and integration services to derive maximum benefits from these systems. Many automation suppliers also provide equipment for building operations and controls. Therefore, because of the use of communications standards, connecting automation and building automation systems is easier than it was a decade or more ago.
Rather than begin an integration project with a single automation supplier—unless you are primarily a “single-vendor shop,” or have your own engineering department—it may make sense to contact a system integrator or engineering house that has experience with several automation vendors and their systems. This is especially true if you want to connect your process control systems and/or manufacturing execution systems (MES) (aka manufacturing operations management (MOMs)) with your building management systems (BMS).
AE (architecture and engineering) firms have their own automation/controls engineering houses, and you’ll find them capable of providing full lifecycle consulting, definition, integration and support services for layer 3 and 4 information systems, according to Alan Stanfill, director, digital transformation, Gray Solutions, a Gray Company.
These system houses also provide control systems integration and consulting services for new and existing food and beverage facilities, says Jim Vortherms, CRB senior director, automation delivery. Services include, for example, automation (PLC and HMI development); SCADA with OEM skid integration; operational technology; data collection, reporting, and analysis; and integration with external systems such as MES, LIMs, BMS, ERP, et al.
System integrators (SIs) often work with AEs and have expertise not only with industrial automation systems but also BMS and most other systems in a food plant. Polytron, a Control System Integrators Association Certified Member, helps manufacturers develop and implement their digital transformation strategy and road map, which includes integrating data from all of the different manufacturing systems into one contextualized source of information, according to Richard Phillips, PE, PMP, director of smart manufacturing.
Modern MOMs more easily integrate with process control, BMS, and most all other systems within a manufacturing facility. Building temperature, humidity and other conditions can have an impact on productivity, product quality, shelf life, packaging materials and many other key facets of manufacturing, so having real-time insights into these conditions is key, adds Phillips.
Today, a new facility should be designed with integration in mind, says Vortherms. For existing facilities, an engineer needs to understand what it takes to bring systems together and integrate information into operations. Every project is unique, requiring research into owner needs and objectives as well as the appropriate technology for the application to determine the correct solution.
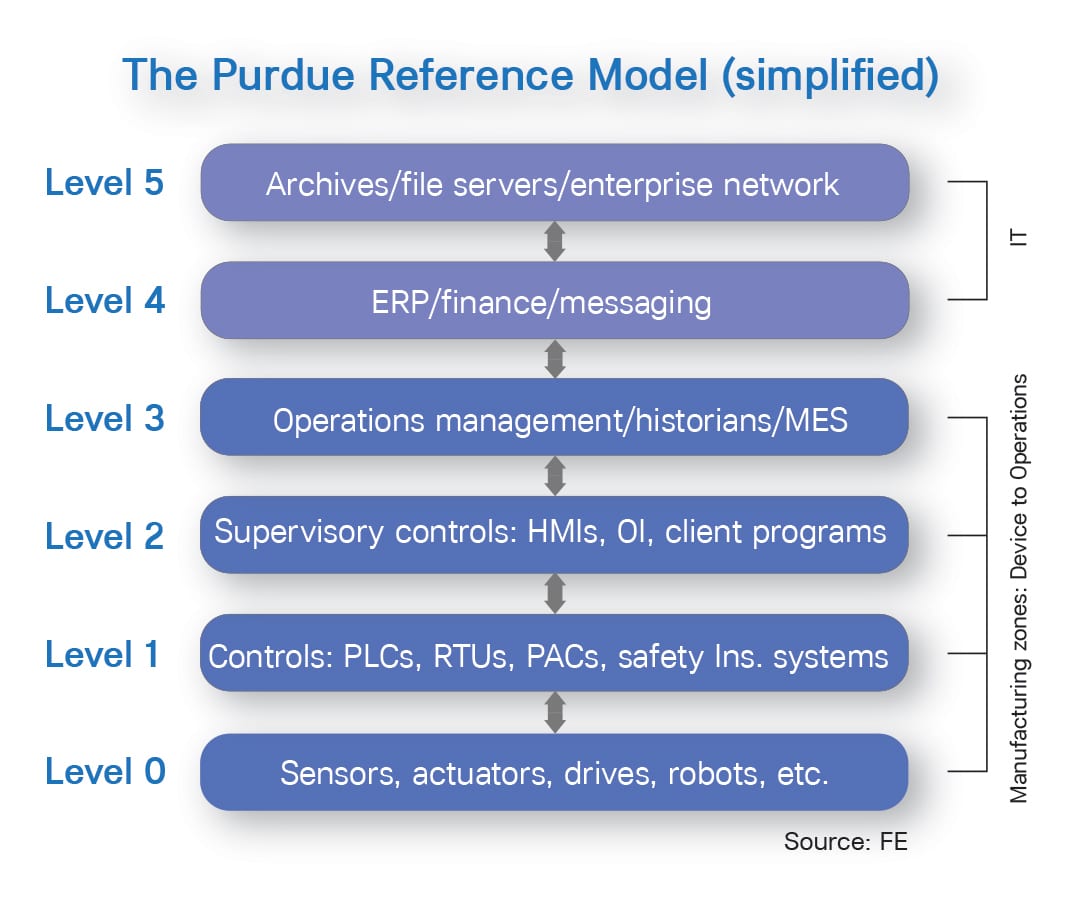
Engineering houses and system integrators know how to connect together all levels of a plant-wide network so it can operate as a single, connected machine for making food or beverages. Today, levels 0 through 2—and sometimes 3—will be similar for both industrial automation and building automation networks, however, they “speak” different protocols, which can be “translated” with gateways and protocol converters to make an integrated and connected network.
What Can Be Accomplished
I asked our panel of experts to name some applications that lend themselves to integration of facility systems, and they range from reasons and type. For example, Stanfill notes that one food processor client wanted to integrate process controls and energy management and utilities (gas, water, electricity) to understand production costs by pound of production.
“For one of our customers that produces fruit/vegetable smoothies and other drinks, we integrated multiple systems during the manufacturing and transportation of the product to ensure the temperature profile during the entire time was within the quality control guidelines that would allow the product to have the shelf life expected before being consumed,” says Phillips.
CRB’s Vortherms listed a few applications:
• Energy management in vegetable oil refining to determine the cost inputs as well as being able to appropriately allocate those costs to the processing units.
• Utilities management, specifically steam utilization, in a process unit to optimize and reduce the amount of steam being used, thereby reducing steam generation costs. Return on investment for these projects was significant with timeframes of 9 to 16 months.
• Process area temperature controls in a pea protein processing facility. A tie-in was done between the process control system and the building management system to stop the intake of -20°F outside makeup air when the process was not running.
• Process area ambient temperature and humidity and what effect that has on liquid reactive resin production quality.
• OT network log anomaly monitoring and analysis to identify protentional network issues before production upsets.
"Integrating manufacturing systems with building management systems is more easily accomplished now than a decade ago due to the more open nature of modern systems including standards for integration." — Richard Phillips
Why Integration? Because it’s Doable Today
Ten or fifteen years ago, processors may have had process controls and BMS in the same control room, which made it easier for operators to manage HVAC, boilers and process controls—though they weren’t “wired” together. See “Fabulous Food Plant: FAGE Yogurt.” Certainly, that was more convenient than having the controls for each in two separate rooms. Today, while processors may have process controls and BMS on the same tablet or PC, they are beginning to see that the seamless integration of process controls and BMS is doable—and desirable.
“This integration is increasing in popularity primarily since users realize it’s now within the realm of possibility,” says Gray’s Stanfill. “Modern data platforms are much more modular and flexible than was previously the case with islands of automation and information. This enables more rapid and flexible integration between systems.”
“Integrating manufacturing systems with building management systems is more easily accomplished now than a decade ago due to the more open nature of modern systems including standards for integration,” says Polytron’s Phillips. “For some industries, this integration is more critical and brings more value than for other industries, but the ease of integration is still there.”
CRB’s Vortherms sees a definite trend toward integration. “Requests to integrate the process control and facility control systems are desired by owners and becoming more frequent on projects and in RFPs. Companies are asking for integration between the process control and facility systems as a way to dial in costs, better manage resources and improve product quality.”
Communication between the various systems for process control, building management systems, energy management systems and utilities has become easier to accomplish through industry adaptation of open and standardized communications protocols. Additionally, new technologies such as protocol converters or gateways ease the translation between various systems and protocols, adds Vortherms. Integration of process and facility controls is typically easier to accomplish on new or modern facilities because they typically have the necessary infrastructure built in to facilitate the services and systems. These include site-wide networks for both OT and IT, wireless, security, server infrastructure, etc. An existing site may need to build these services and solutions or upgrade systems before being able to take advantage of integrations, says Vortherms.
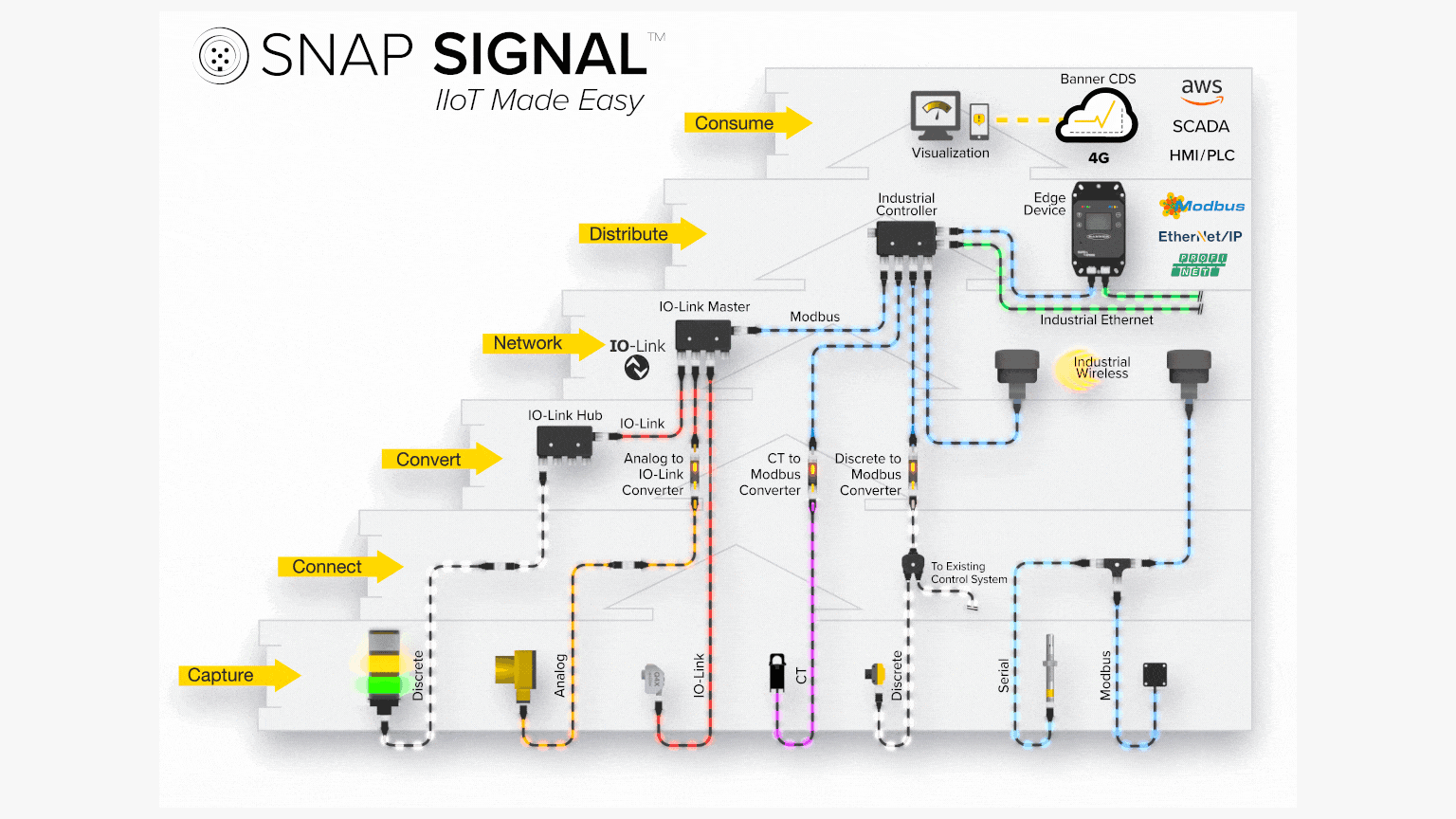
Since building automation equipment typically runs BACnet or other BMS-specific protocols and doesn’t talk to automation networks, another method is needed to link to process networks. Banner Engineering’s SNAP SIGNAL platform uses an “overlay network” to bring BMS data to a separate automation network. An overlay network doesn’t disturb the original building network or change its architecture. Photo courtesy Banner Engineering
Perceived Benefits of Integration Are Real
Energy—and understandably so—is a big reason for integrating all these systems. “For food/beverage processors specifically, this tighter integration provides opportunities for energy management, better quality control and reduced downtime to name a few,” says Polytron’s Phillips. “Energy management is a big opportunity, as we all know, due to not only the cost of energy but also demands for lowering carbon footprint and meeting sustainability goals. Turning off systems that do not need to be running is one easy way.”
As we noted, too many times building management systems are in different areas of the plant where there is no visibility into how or if they are running. So having real-time information and integrating with these systems provides an easy way to better optimize their use. In addition, downtime from any building utility such as electrical, compressed air and cooling can have a significant impact on production. For this reason, many times these systems provide the highest ROI opportunities for monitoring solutions, such as predictive maintenance, that help detect potential failures before they occur, adds Phillips.
“We have dealt with a client who wanted to be able to break down costs (energy as an example) by unit of production,” says Gray’s Stanfill. An example is a food processor who can now assign costs for water, gas and electric, along with other factors, by pound of production. This is a powerful metric to understand their true cost of production in order to be competitive in the market, says Stanfill.
But energy isn’t the only reason to integrate systems. “Food processors are benefitting from a higher quality product,” says CRB’s Vortherms. “Controlling the room environment helps eliminate atmospheric conditions, such as temperature and humidity, from affecting the product quality.”
With the integration between the process control system and the building management system, clients should recognize energy savings if the process area does not require a controlled environment when the process is not running. In such a scenario, there is no reason to condition the space if not required.
Clients are looking to get the most from their production investments. Integration creates opportunities to improve product quality, production uptime and capacity, operator effectiveness, etc., adds Vortherms.
Quantifying Results
Processors will want to know how they can quantify results from a BMS/controls integration. “It’s really important to identify key metrics clients want to track,” says Stanfill. “Water usage or quality may be a much larger factor to one customer than another, for example. Once they determine what matters most to them, which we often help them determine, the focus shifts to showing a metric that can be impacted. This can vary at different levels of an organization, so it’s critical to show how metrics can be impacted with choices and actions. This is both empowering to the team and leads to results.”
“If the goal of the integration is energy or utility savings, return on the investment can be determined through collection of baseline data on the process as well as inputs, calculation of the expected savings, and then comparison of actuals to expected,” says Vortherms.
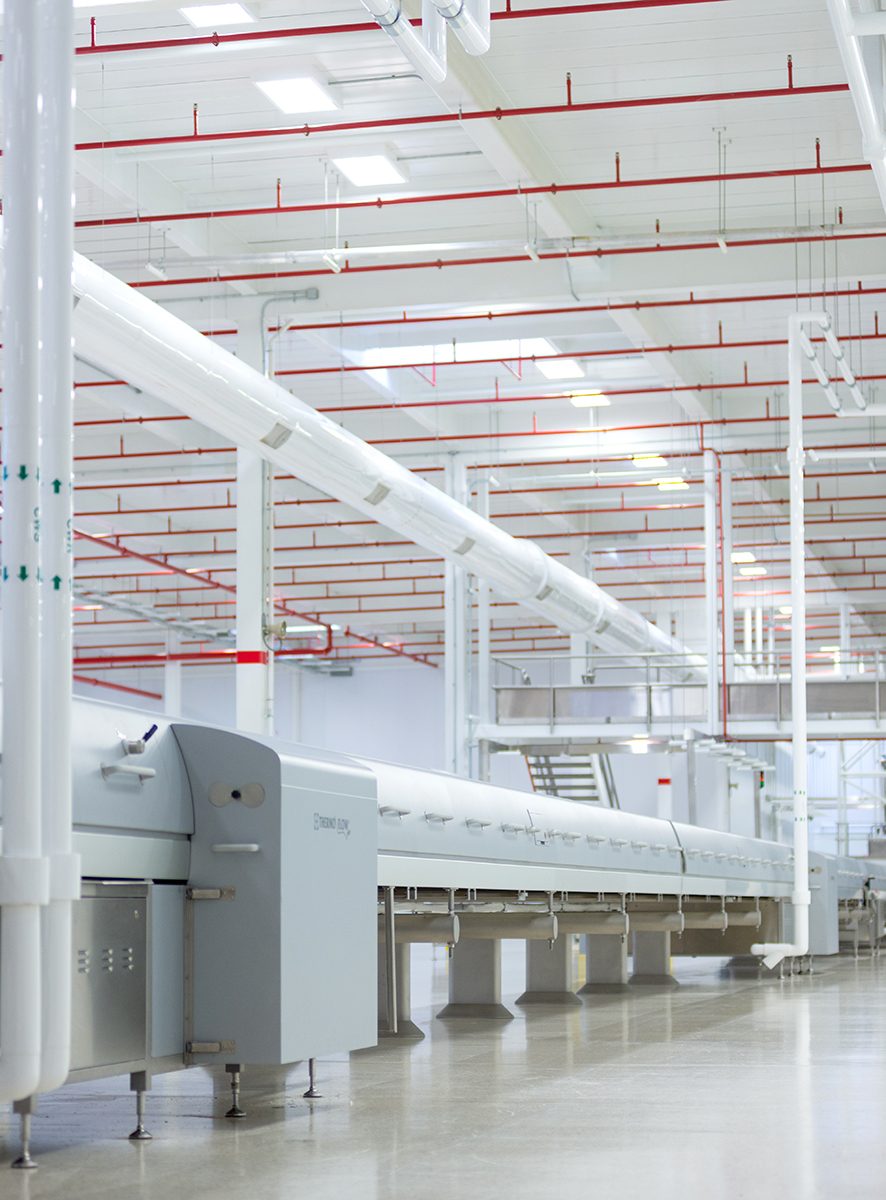
Chocolate bars are cooled under cover where temperature is controlled. However, for more efficiency, ambient room temperature and humidity need to be held at a consistent level by the BMS. Photo courtesy Imagemakers Inc.
Generally speaking, today’s technology is making it easier for building controls, maintenance groups and process control engineers—and the IT staff—to work together on integration projects. The interviewees share their comments:
Today’s environment makes it easier to work together and even to get IT buy-in, which is needed to comply with company standards and needs. This is helped by more modern information platforms that work better with corporate IT, manage data more securely, and are also more open to IT standards. —Alan Stanfill, Gray Solutions, a Gray Company
Both maintenance and controls engineers usually support production and associated systems, so working together to provide the necessary integration between any plant system is typically not an issue. Stakeholder alignment to properly identify the problem/opportunity and develop a plan that everyone is aligned with to solve the problem is usually the first step. After this, it’s a matter of budget and execution. Bringing IT into the team helps ensure their guidelines are followed and allows them to provide any support needed from their side. —Richard Phillips, Polytron Inc.
The key to making this type of integration a reality is early discussions and communications between the various groups involved in the systems. Open communication builds a level of trust and helps all to understand this effort is to work together and not for one group to take over another’s domain. In addition to building a level of trust, it’s incredibly important to have management buy-in. Without this support, it will be incredibly difficult to unite groups, foster trust and successfully integrate. Who is managing the various networks in a facility will determine if IT or OT will need to be involved. Normally, projects will require networking configuration and or changes to the network as the most common communications protocols today are Ethernet based.
Finally, the production quality team will need to be involved. It is critical to understand how environmental conditions might affect production, maintenance, and people. Also, consider the cost to remediate or adjust for environmental conditions. —Jim Vortherms, CRB
Getting All Departmental Teams on Track and on the Same Page
“Developing the ROI for a planned project/initiative—then measuring the actual ROI after the project has been implemented—is typically one of the better ways to quantify results,” says Phillips. “For example, a plant’s energy usage over a given period is X. An energy management project is implemented to turn off systems when they are not needed. The plant’s energy usage can then be measured again after the project to determine cost savings and ROI associated with the cost of the project.”
CRB has worked on multiple energy savings projects that have been successful, says Vortherms. The success of the project has been to reduce the energy costs and the amount of energy used through optimization. The actual ROIs for these projects beat the calculated, expected ROI.
Final Thoughts
“Focus on projects with a solid business driver and expected benefit,” says Phillips. “Make sure to quantify the benefit and gain alignment from all of the stakeholders that the project will impact as they will help ensure the project is successful. Start with small projects that can provide big wins, then build on that. When possible, avoid taking on scope where the project gets out of hand, takes too long to implement and becomes difficult to show the benefits.”
“Think outside the box,” says Stanfill. “What may have been a real challenge just a few years back may have a more modern approach that makes it much more easily achievable today. Don’t look for the big bang approach to integration and implementation. It’s typically more impactful to select areas that will provide tangible value before progressing to the next.” FE
Resources:
“Linking process control with building control and HVAC systems for better control,” FE, July 21, 2020, Wayne Labs
“Digital transformation relies on smart sensor data and human inputs,” FE, April 20, 2022, Wayne Labs
“Increase insights and efficiency with smart instrumentation,” FE, March 27, 2022, Ola Wesstrom
octoBER 2022