Dry Processing - part 1
Safe In Processing Dry Products?
Is Your Facility
Unlike wet ingredients, the handling of dry powder ingredients and products usually requires specifically designed process areas to prevent dangerous situations that could result in worker injuries or death.
According to “Dust Safety Science,” the food products industry accounted for 48.4% of all fire and explosion incidents in 2022. In general, dust collectors were identified as the primary source of combustible dust problems, accounting for 24% of the incidents. Storage silos (21.1%) and dryers (20.7%) were also significant contributors.
Whether a processor is in a new facility designed to handle dry ingredients and products or an older structure that was once right-sized and fitted to handle the job in the past, new market demands often create the need to throw in more equipment and processes faster than they can be acclimated in the building. When this involves powders from grinding, sifting or mixing operations—or just plain material movement—facilities may no longer be able to handle the process safely and efficiently. Flammable dust that once was easily removed from the environment hangs around and accumulates where it shouldn’t. And due to inadequate training, the clean-up crew sometimes misses areas where dust accumulates.
Be sure your dry processing facility is up to date, meeting NFPA rules and has the latest and safe dry processing equipment that prevents fugitive dust emissions that could result in a fire. Image courtesy of José Alfredo Velázquez from Pixabay
by Wayne Labs
“We have seen a number of facilities grow over the years by buying additional pieces of equipment and self-integrating them without working with a qualified integrator,” says Joshua Allen, process engineering manager for AD Process Equipment, a Gray Company. “When this occurs, a complete risk assessment is often not performed to fully understand the impact on the existing systems and the additional hazards that can be introduced to the facility. Improper repairs and maintenance on older equipment and repurposing of equipment for processes it was not intended have also been identified as leading to potentially dangerous situations.”
The Problems with Older Facilities
Typically, older facilities may have issues such as outdated ventilation systems, insufficient dust control measures and inadequate pressurization in critical areas, says Dennis Collins, CRB’s architectural discipline leader based in St. Louis, who is also a senior associate at CRB. “One common problem we observe is with the pressurization in rooms where raw materials are handled. Often, these rooms have negative air pressure, which allows outside air to infiltrate the processing areas. This can introduce contaminants and compromise the safety and quality of the materials being processed.”
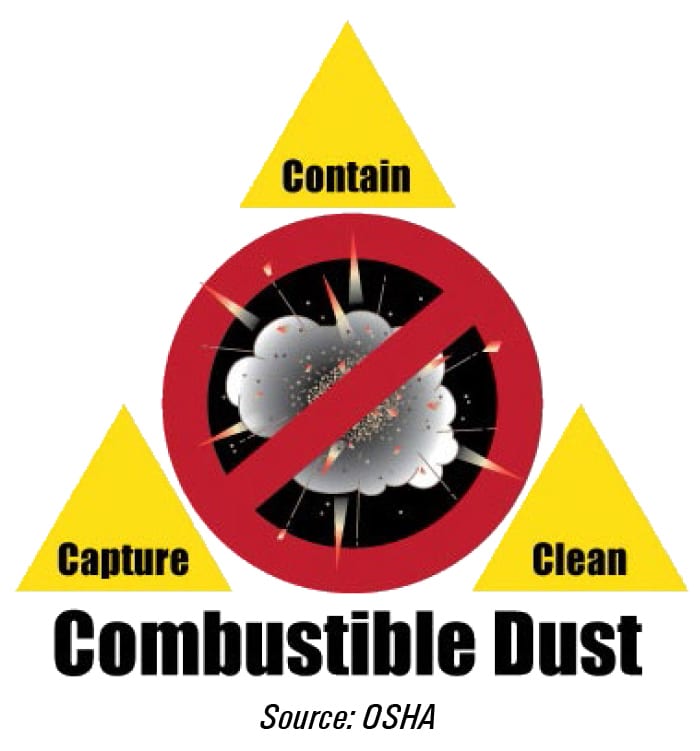
OSHA created a combustible dust triangle showing key ways to minimize the potential of a dust explosion The three are (1) capture dust before it escapes into a work area; (2) contain dust within equipment, systems or rooms built to safely handle the dust; and (3) clean work areas, overhead and concealed spaces. Image courtesy of OSHA
Improving these facilities often requires a comprehensive assessment of the entire facility to identify all areas needing upgrades, adds Collins. “Addressing pressurization issues, for instance, involves not only correcting the airflow but also ensuring that the entire ventilation system is up to modern standards. This may include installing advanced filtration systems, upgrading HVAC systems and implementing better dust control technologies.”
Older facilities often house older equipment, says Adam Dittbenner, instrumentation manager at Interstates, a CSIA (Control System Integrators Association) certified member. This equipment has typically been in continuous, or near continuous, operation for a considerable amount of time, as well as in harsh environments. This equipment needs to be checked occasionally if it is to be relied upon for detecting hazardous situations in the facility (“Haz Mon” systems). In regard to power distribution equipment, dust often accumulates in electrical panels and gear over the course of time, as well. This dust needs to be cleaned out, and electrical gear needs to be checked to ensure it still operates properly. These checks include inspecting for good internal contacts and adequate insulation of energized parts, plus testing the ability to trip at the proper time to provide protection of downstream equipment.
Fast and Cheap — Not a Good Idea in Dry Processing Applications
Hazards are often created when the mindset is, “We can do this fast and cheap.” A recent example is a customer who wanted to install a mill to grind sugar. They had a good supplier for crystallized sugar and didn’t want to pay the premium for confectionary sugar. They found an inexpensive mill online from an international supplier at a very low cost.
While at their facility for another project, our team discovered that they were installing that capability as well and asked about upgrading the controls to their standards. Through further discussion, we learned they were unaware of the hazards associated with the new dust they would be creating and that they could not route it to their existing dust collection unit. It was also found that the wiring on the unit did not comply with the new hazardous classification area they would be creating by operating it as the manufacturer intended.
We were able to assist them in correctly identifying the risks and provided a solution that would allow them to mill their own confectionary sugar, but it was a much larger project than it would have been if they had been working with us from the beginning to help ensure that the equipment was properly specified to meet their safety requirements.
—Joshua Allen, Process Engineering Manager, AD Process Equipment, A Gray Company
“Sometimes older systems are not ideally sized or have been purchased from a legacy customer and are not being used for what they were originally intended,” says Brian Shoop, director of process and packaging, Gray Solutions, a CSIA certified member.
“The primary issue with older facilities is that they were not designed with the latest NFPA codes in mind, which means they often lack adequate explosion venting and isolation systems,” says Zac Ulmer, senior process engineer at Gray Solutions. “Older facilities usually have dust collection points meant for comfort rather than safety. To improve them, we often need to retrofit existing systems with modern dust control technologies, ensuring proper venting and isolation to prevent dust explosion propagation. It is a case-by-case decision whether retrofitting or rebuilding is necessary, but safety is always the priority. We work with our customers to lay out all the options for their consideration and work with them to make the best decision.” End of Part 1