Dry Processing - part 2
Safe In Processing Dry Products?
Is Your Facility
Unlike wet ingredients, the handling of dry powder ingredients and products usually requires specifically designed process areas to prevent dangerous situations that could result in worker injuries or death.
New Equipment to the Rescue?
It may seem that dropping in new and safer dry processing equipment could be a way to rescue an existing dry powder facility that might not have all the accoutrements needed for safe operations. But, wouldn’t it be safer to rip and replace or build a new facility designed to safely handle dry processing applications from the get-go?
“Hazard monitoring systems and power distribution systems can be replaced, however they are often very integral to a facility,” says Interstates’ Dittbenner. Replacement of them requires electrical installation effort in addition to the new equipment. Performing maintenance on existing systems and ensuring they operate properly is typically a lower spend compared to replacement, and also allows for getting the full life out of the equipment.
Be sure your dry processing facility is up to date, meeting NFPA rules and has the latest and safe dry processing equipment that prevents fugitive dust emissions that could result in a fire. Image courtesy of José Alfredo Velázquez from Pixabay
by Wayne Labs
Obviously, a new facility designed from the ground up specifically for the task is the safest thing to do, says AD Process Equipment’s Allen. “However, that is very expensive and time-consuming. There are often solutions that can be integrated into or added to existing facilities to help mitigate risks. Each situation is unique, and the important thing is to work with a qualified team that can identify and assess the risks and provide solutions.”
“While dropping in new equipment can improve safety, it is often highly site-specific and may not address all underlying issues of an existing facility,” says Gray’s Shoop. “Retrofitting can sometimes be more costly and complicated than building a new facility. Using tools like 3D scanning and virtual design coordination helps us assess the feasibility of retrofits before any physical changes are made. Ultimately, building a new facility allows for better placement of vents and equipment to meet NFPA codes and ensure optimal safety and efficiency, but that isn’t always the best answer.”
“It’s really that upfront analysis that will help you manage your risk—and does it make sense because, you know, even building a brand-new facility comes with its own risks,” says Ulmer.
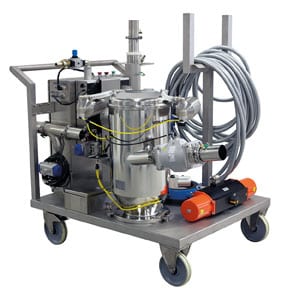
The ATEX-certified INEX (inert explosion-proof) pneumatic vacuum conveying system from Volkmann USA, features an optional mobility package. Setting the entire conveying system on a self-contained, rolling platform, the mobile INEX system enables other processors to safely convey dry and wet powders in hazardous environments where explosive vapors may be present. Image courtesy of Volkmann USA
Improvements in Dry Processing Equipment
There have been many improvements in the availability of equipment and controls designed and rated for use in hazardous locations, says Allen. “In the past, many systems relied on pneumatic spring scales in the hazardous environment. Now, we can install full instrumentation and load cells in hazardous environments, similar to how they would be utilized in non-hazardous situations. The key is working with the right team that can determine the risk, choose the appropriate level of controls required and provide them in a manner that they operate as intended. It should also be noted that educating employees about the risks and requirements plays an important role in ensuring that the equipment continues to operate safely once it is installed. Rated instrumentation, for example, must be reassembled according to design to maintain its integrity (you have to replace the O-ring if you lose it!).”
Special NFPA Note: NFPA 660 — Inclusive Standard for Combustible Dusts
NFPA 660 is in the Fall 2024 cycle due to the Combustible Dust Document Consolidation Plan (consolidation plan) as approved by the NFPA Standards Council. As part of the consolidation plan, NFPA 660 is combining Standards NFPA 61, NFPA 484, NFPA 652, NFPA 654, NFPA 655, and NFPA 664. For consolidated draft and revision cycle information, see the “Next Edition” tab on the linked web page.
“Recent advancements in robotics and equipment for handling, processing and conveying dry products have brought significant improvements in both safety and efficiency, making them valuable investments for both older and new facilities,” says CRB’s Collins. Some notable advancements include:
• Explosion suppression systems: A large safety improvement, these systems detect and suppress potential explosions in their early stages, significantly reducing the risk of catastrophic events.
• Advanced robotics: Robots have become equipped to perform tasks such as grinding, mixing and packaging with greater accuracy and speed, reducing human error and increasing overall efficiency.
• Precision mixing equipment: Advanced mixing equipment with improved control systems allows for precise blending of ingredients, ensuring uniformity and consistency in the final product.
One notable improvement is the use of enclosed bagging lines, which contain dust and improve safety by keeping operators away from dust exposure, says Gray’s Shoop. Additionally, slow-moving mechanical conveyors like “chainveyors” are replacing bucket elevators, reducing dust generation and improving safety. Robotics and automation have also advanced, particularly in packaging processes, where they enhance precision, reduce manual handling and minimize dust exposure. Technologies like hyperspectral imaging for raw material inspection can also improve safety and quality control.
Finally, before making any changes to your facility to accommodate new equipment, it’s a good idea to review the guidelines and requirements of NFPA to ensure mitigation of hazards caused by dust, says Dittbenner. “Interstates can help with reviewing these requirements and applying them to your facility. Sometimes new systems and equipment are needed, and sometimes existing equipment can be made sufficient by checking it and resolving any issues it is currently encountering.”
Evaluate Facilities Before Upgrading Equipment
Processors should engage the services of an experienced firm to evaluate their facilities, says AD Process Equipment’s Allen. Any additions or changes should be performed by firms that have experience and knowledge about working with potentially hazardous situations. Even something as basic as buying a new piece of equipment that a maintenance team can easily install should be evaluated if it will be near or potentially create a hazardous environment.
Evaluating existing facilities and current operational procedures and equipment is crucial when planning improvements for food safety and employee safety, says CRB’s Collins. Processors should conduct a comprehensive review of the facility to identify areas needing upgrades, analyze current processes for efficiency and ensure compliance with food safety regulations. This involves assessing structural integrity, identifying outdated machinery and pinpointing bottlenecks where new technology could enhance productivity and safety.
Deciding whether to renovate, add on or replace a facility depends on the extent and cost of necessary upgrades, the future growth and flexibility of the facility and a detailed cost-benefit analysis comparing the options, adds Collins.
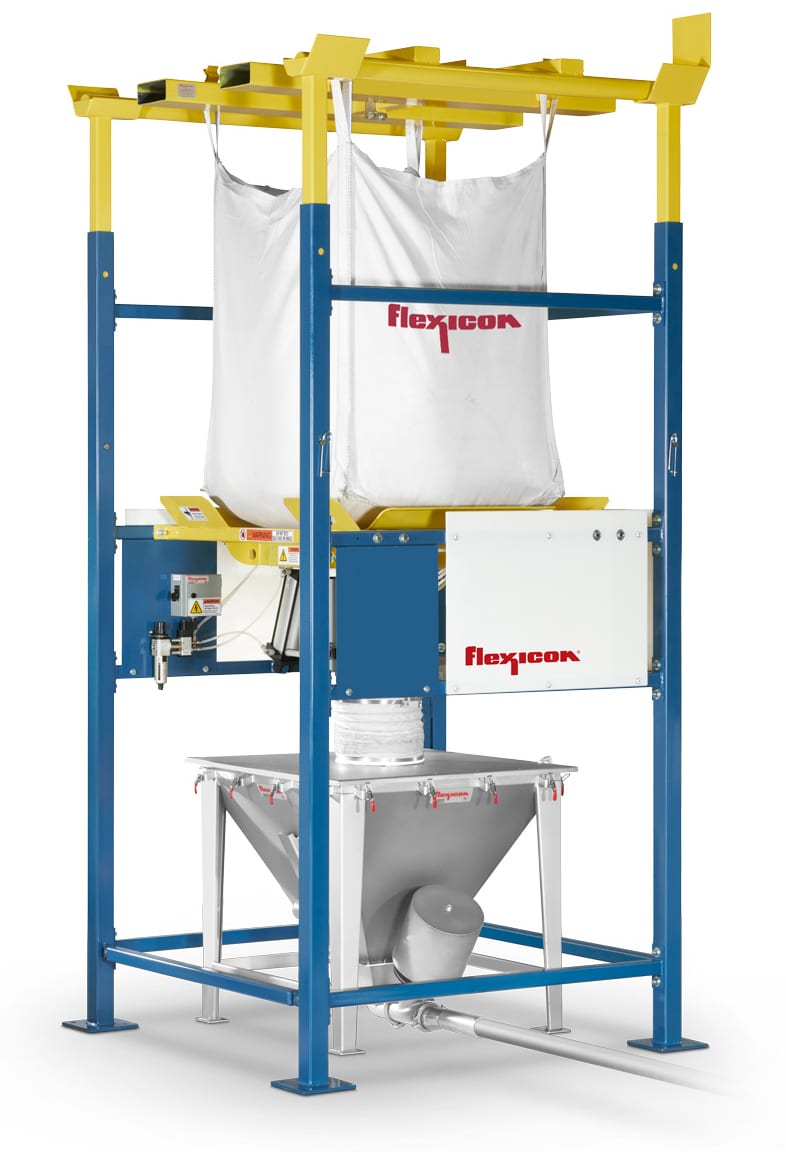
The Flexicon BFF Series Bulk Bag Discharger contains dust when connecting bag spouts and feeding material into vacuum conveying lines, preventing contamination of the product and plant environment. Image courtesy of Flexicon
System Integrators and Engineering Houses can Help with Dry Processing Projects
To operate safely, dry processing applications do need special attention compared to wet food processes. Able to assist with facility, process and packaging design plus implement automation and controls, most facility architects, system integrators and engineers also provide these specialty services geared to dry processing, some of which include:
• Dust studies to assess the flammability/combustibility of powders and risks in a facility
• Turnkey systems for handling material from receiving through packaging finished products
• Design of systems to minimize dust exposure by properly integrating equipment to eliminate potential leaks as well as systems that operate in spaces where, due to certain processes, the risks will exist in the environment
• Integration of dry handling systems with facilities and processes, ensuring safety through proper alarm and shutdown systems
• Design and sizing of rotary feeders and airlocks to act as isolation devices, preventing dust explosions from propagating through ductwork
• Working with clients in the early phases of design to understand the material/product characteristics and ensure safe and effective system implementation
• Design, installation, integration, commissioning and servicing of various hazard monitoring systems to help clients meet NFPA 61 requirements for monitoring of rotating equipment
• Electrical Preventative Maintenance (EMP) services to facilities with dusty processing environments to help clients keep their power distribution system maintained/serviced and in compliance with NFPA 70B
Evaluating existing facilities requires a thorough front-end analysis to manage risks and determine the best course of action, says Gray’s Ulmer. Factors to consider include the current condition of equipment, compliance with NFPA codes and potential safety hazards. Retrofit options should be weighed against the costs and benefits of building new facilities. Often, older facilities may be operating unsafely, and significant upgrades are necessary to meet modern standards. A detailed assessment and cost analysis can help processors decide whether to renovate, add on or replace their facilities.
Stay Safe
An important aspect of dry processing safety is ensuring proper housekeeping and maintenance to prevent dust accumulation, says Gray’s Shoop. “Implementing explosion-proof central vacuum systems can help maintain cleanliness and safety. Additionally, staying updated with industry standards and regulations, such as those from NFPA and insurance carriers, is crucial for maintaining safe operations. Our ability to use advanced tools like 3D scanning and virtual design coordination allows us to address safety concerns effectively and design efficient systems tailored to each facility’s specific needs.” FE